Baustoffe: In grünen Beton gegossen
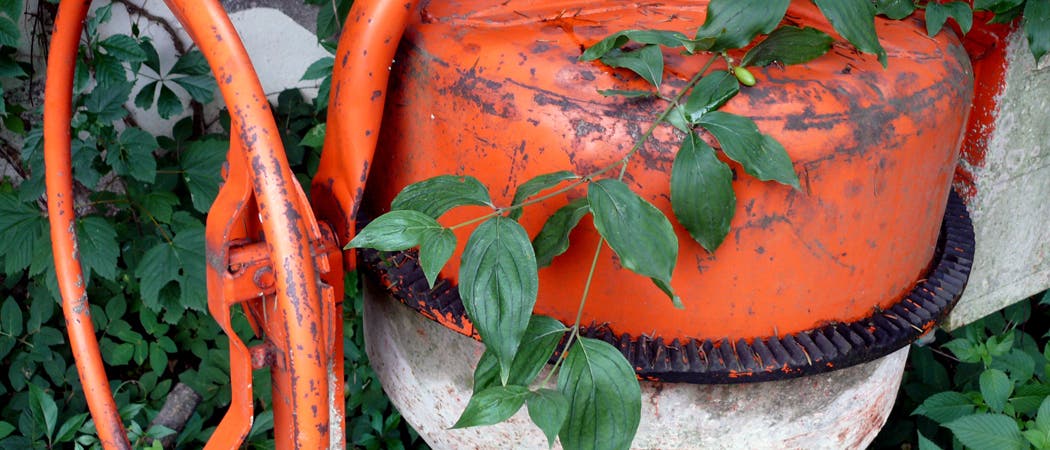
Die Zementfabriken dieser Welt werden 2013 voraussichtlich 3,4 Milliarden Tonnen des geschätzten Baumaterials herstellen. Würde man diese Masse über Manhattan ausgießen, ergäbe sich daraus ein rund 14 Meter hoher, flächendeckender Betonklotz. Im kommenden Jahr dürfte dieser monolithische Block sogar noch größer ausfallen, angesichts des gegenwärtigen Baubooms in Entwicklungsländern wie China und Indien – Zement galt schon immer als wichtiger Rohstoff für unsere Zivilisation: Vom 2000 Jahre alten Pantheon in Rom bis hin zu modernen Wolkenkratzern und Autobahnen hält er unzählige Bauwerke zusammen.
Doch das hat seinen Preis: Zum Leidwesen des Klimas stellt man die heute am weitesten verbreitete Form des Materials, so genannten Portlandzement, durch das Brennen von Kalkstein und Ton in riesigen Öfen her. Bei diesem Prozess entweicht für jede Tonne des Baustoffs nahezu eine Tonne Kohlendioxid in den Himmel. Etwa fünf Prozent aller menschengemachten Treibhausgasemissionen stammen aus der Produktion von Portlandzement.
Diesen Ausstoß zu reduzieren, ist kein leichtes Unterfangen. Denn bei Zement handelt es sich nicht nur um einen weit verbreiteten und massenhaft eingesetzten Rohstoff, sondern auch um einen der komplexesten bekannten Stoffe in den Materialwissenschaften. Von seiner Struktur und Zusammensetzung bis hin zu den chemischen Reaktionen beim Mischen von Zement und Wasser "bleiben einige der grundlegendsten Fragen unbeantwortet", sagt Hamlin Jennings, Leiter des Concrete Sustainability Hub (CSHub) am Massachusetts Institute of Technology in Cambridge. "Es wird lebhaft diskutiert, was im Detail passiert, wenn Wasser mit Zementpulver in Berührung kommt", fügt Zementexperte Kenneth Snyder vom National Institute of Standards and Technology in Gaithersburg, US-Bundesstaat Maryland, hinzu. "Man führt beinahe Glaubenskriege darüber."
Die Ankündigung von Kohlenstoffdioxidsteuern sowie der Emissionsrechtehandel haben Industriekonzerne auf der gesamten Welt allerdings dazu gebracht, sich für eine grüne oder nachhaltige Zementproduktion zu engagieren. Ihre Ansätze sind vielfältig – sie unterstützen die Grundlagenforschung ebenso, wie sie darauf drängen, internationale Bauvorschriften zu reformieren. Falls erfolgreich, ließe sich der CO2-Fußabdruck der Zementindustrie um die Hälfte zu senken. Zement zu verstehen, das ist das Ziel – von seiner Funktionsfähigkeit in verschiedensten Strukturen bis hin zu seinen quantenmechanischen Eigenschaften. "Es ist ein hartes Geschäft", sagt Jennings: Die Gründe dafür würden klarer, wenn man sich bewusst mache, was bei der Zementproduktion auf molekularer Ebene geschieht.
Seltsames Gemisch
Am Anfang eines jeden Zements steht ein Gemisch aus Kalkstein und Aluminiumsilikat-Tonmineralen. "Jede Zutat besitzt ihre eigene Chemie und andere Fremdstoffe", erläutert Jennings. Werden die Rohmaterialien in einem Ofen zusammen auf etwa 1500 Grad Celsius erhitzt, reagieren sie in vielfältiger Weise miteinander. Schließlich entstehen graue, murmelgroße Klumpen, die man als "Klinker" bezeichnet. Sie enthalten Silikate, Eisen- und Aluminiumoxide (die hauptsächlich aus dem Ton stammen) sowie Kalziumoxide. Letztere entstehen, wenn Kohlenstoffdioxid durch Wärmezufuhr aus dem Kalziumkarbonat des Kalksteins herausgelöst wird. Dieses CO2 macht einen Großteil der Emissionen bei der Zementproduktion aus, der andere geht auf das Brennmaterial des Ofens zurück. Sobald der Klinker abgekühlt ist, wird er gemeinsam mit Gips – die Menge bestimmt, wie schnell der Zement später aushärten wird – zu einem feinen Pulver mit einer mehlähnlichen Konsistenz gemahlen und zu einer "Mischanlage" weiterbefördert.
Dort wird das Zementpulver mit Wasser zu einem Brei vermengt, dessen Konsistenz vom Verwendungszweck abhängt – ob für einen Brückenpfeiler oder eine Fahrbahndecke. In den meisten Fällen wird die Masse mit Sand, Kies oder größeren Steinen zu Beton verarbeitet. Der Betonschlamm wird dann per Lastwagen zur Baustelle transportiert und in eine Form gegossen, wo er schließlich aushärtet. Dieser Prozess beginnt zwar recht schnell, kann dann aber Monate andauern.
"Eines der Mysterien und Gegenstand intensiver Forschung ist, dass die Zementmasse in den ersten paar Stunden flüssig bleibt, bis plötzlich eine Reihe von chemischen Reaktionen gleichzeitig einsetzt, deren Folgeprodukte zum Aushärten führen", erläutert Jennings. Entscheidend für das spätere Material sind Hydratationsreaktionen, die das Wasser und den pulverisierten Klinker in künstliches Gestein verwandeln: ein Gerüst aus Kalziumsilikathydrat (CaO-SiO2-H2O oder C-S-H). "Alle Betonbauten auf diesem Planeten basieren auf diesem Übergang von einer Flüssigkeit zu einem Gestein", sagt Roland Pellenq, der sich am CSHub mit physikalischer Chemie beschäftigt.
C-S-H sei jedoch eine unerträglich ungenaue chemische Formel, beklagt sich Pellenq. Seine Bestandteile haben kein festgelegtes Mengenverhältnis, und die Reaktionsprodukte in einer aushärtenden Betonprobe hängen von den anfänglichen Zutaten ab – der verwendeten Wassermenge, dem Verhältnis von Kalzium zu Silizium sowie von speziellen Zusätzen, Fremdstoffen, Temperatur und Luftfeuchtigkeit. Und natürlich ist Beton undurchsichtig, was die Analyse von C-S-H im Moment des Entstehens zusätzlich erschwert.
Rezeptur verbessern
Trotz dieser Herausforderungen, sagt Pellenq, machten er und seine Kollegen vom CSHub Fortschritte hinsichtlich der CO2-Emissionen. In einem viel versprechenden Ansatz versuchen die Wissenschaftler die Brenntemperaturen und damit den Brennstoffverbrauch zu senken. Dabei konzentrieren sie sich vor allem auf die Mineralien Alit und Belit, zwei der Hauptkomponenten von Klinker, durch die sich C-S-H überhaupt erst bilden kann. Alit (Ca3SiO5) ist der reaktionsfreudigere Stoff von den beiden: Nach der Zugabe von Wasser härtet er innerhalb von Stunden aus und verleiht dem Beton so seine anfängliche Festigkeit. Doch während Alit erst bei 1500 Grad Celsius entsteht, formt sich Belit (Ca2SiO4) bereits bei rund 1200 Grad Celsius. Belit erstarrt zwar letztlich zu einem härteren Material, benötigt dafür aber Tage und sogar Monate – zu lang, um in Bauprojekten allein zum Einsatz zu kommen.
Pellenq und seine Kollegen erforschen, ob sich einige Kristallstrukturen des Minerals vielleicht genauso reaktionsfreudig verhalten wie Alit und gleichzeitig bei niedrigeren Ofentemperaturen entstehen können, um Brennstoff zu sparen. Eine entscheidende Rolle bei dieser Suche spielt die atomare Ebene, etwa die Elektronenverteilung im Belitkristall. Mit Hilfe von quantenmechanischen Berechnungen prüfen die Wissenschaftler, wie die Struktur von C-S-H durch Aluminium, Magnesium und andere Verunreinigungen beeinflusst wird [1]. Oder wie Pellenq es ausdrückt: "Um Quanten-Klinker-Engineering betreiben zu können, muss man wissen, wo die Elektronen sind."
Die Forscher am CSHub fanden heraus, dass sich eine Fläche der Alitkristalle stets leichter in Wasser löst als die anderen. Bei Belitkristallen verhalten sich dagegen alle Seiten ähnlich – und der Kristall ist weniger reaktionsfreudig mit Wasser [2]. Aus diesem Grund härtet Belit langsamer aus als Alit. Die Ergebnisse legen allerdings auch nahe, verrät Pellenq, dass bestimmte Fremdstoffe – wie etwa Magnesium – dazu beitragen könnten, dass sich Belit besser in Wasser löst. Dadurch wird er vielleicht schnell genug fest, um sich als Hauptbestandteil von Bauzement zu eignen.
Doch dieser Schritt würde neue Probleme aufwerfen. Denn Belit in Pulverform zu bringen, würde laut Franz-Josef Ulm vom CSHub und seinem Team wiederum vier- bis neunmal mehr Energie kosten als bei Alit. Und das könnte die Vorzüge von belitreichem Klinker bezüglich der CO2-Emission wieder wettmachen.
Das alte Rom als Vorbild
Andere Zementunternehmen, wie etwa Ceratech in Alexandria im US-Bundesstaat Virginia, suchen dagegen nach Alternativen zu herkömmlichem Klinker. Inspiration holte sich die Firma bei einem Zement, den Ingenieure vor 2000 Jahren im antiken Rom verwendeten. Der wichtigste Inhaltsstoff war Puzzolan – Vulkanasche, die mit Wasser zu Zement reagiert und damit als natürlicher Klinker fungiert. Ceratech nutzt eine industrielle Version des Puzzolans: die winzigen Partikel der Flugasche, die man aus den Rauchgasen von Kohlekraftwerken filtert. Allein in den USA produzieren Kraftwerke jährlich rund 70 Millionen Tonnen Flugasche, wovon ein Großteil auf Deponien lagert. Ceratech wandelt die Asche in Zementpulver, indem es sie mit mehreren firmeneigenen Zusatzstoffen vermengt. Da bei diesem Verfahren keine Wärme benötigt werde, so das Unternehmen, sei der Zement aus Flugasche praktisch klimaneutral.
Seit Jahren werden bereits Zementmischungen mit bis zu 15 Prozent Flugasche hergestellt, doch Ceratechs Rezepturen bestehen zu 95 Prozent aus den Resten der Stromproduktion und zu fünf Prozent aus flüssigen Zutaten, berichtet der stellvertretende Vorstandsvorsitzende Mark Wasilko. Darüber hinaus sei der aus Flugaschenzement gefertigte Beton härter als die konventionelle Sorte, so dass man weniger davon einsetzen muss. Dem Unternehmen zufolge ließe sich mit Flugaschenzement das Gesamtvolumen des benötigten Betons in einem typischen dreistöckigen, 4600 Quadratmeter großen Gebäude um 183 Kubikmeter senken – und die Gesamtmasse von Betonstahl um etwa 34 Tonnen. Zudem würden in diesem Fall 374 Tonnen Flugasche nicht auf Deponien landen und die Kohlendioxidemissionen um 320 Tonnen reduziert.
Derzeit, betont Wasilko, spiele Ceratech nur eine kleine Rolle in der Zementindustrie. Und ihr Ansatz zur Verringerung des CO2-Ausstoßes entspreche lediglich einem einzigen Klinker in einer Multi-Milliarden-Tonnen-Mischanlage. Für weit reichende CO2-Reduktionen muss die Baubranche mit ihren Tausenden von unabhängigen Herstellern, Ingenieuren, Architekten, Stadtplanern und Bauaufsichten den Zement der nächsten Generation erst einmal annehmen. Das von den Verbrauchern wahrgenommene Risiko bei der Wahl des umweltfreundlichen Zements gegenüber dem bewährten, konventionellen Pendant muss ohnehin gemindert werden. Die Sorge scheint zu sein: "Wenn das nicht funktioniert, macht mein Chef mir die Hölle heiß", sagt Snyder.
Diese Haltung könnte sich ändern, wenn mehr Länder eine CO2-Steuer oder Programme für den Emissionsrechtehandel einführen. Dadurch käme der Kohlendioxidausstoß viel teurer zu stehen als heute. Ein greifbareres, kurzfristiges Mittel, um die Zurückhaltung zu überwinden, bieten Musterbauten wie Brücken, Straßen und Gebäude. Denn so ließe sich die Funktionsfähigkeit des neuen Zements und Betons auch in der Praxis unter Beweis stellen. Ceratech wirkt jedes Jahr an mehreren Dutzend Projekten mit wie Dockanlagen im Hafen von Savannah und Auffangbecken für Chemikalien der Firma Gulf Sulphur Services in Galveston. Wasilko hofft, dass diese Bauwerke dem Werbezweck dienen.
Es gibt jedenfalls gute Gründe, sofort loszulegen. In den acht Minuten, in denen Sie diesen Artikel gelesen haben, pusteten die Zementhersteller weitere 30 000 Tonnen CO2 in die Atmosphäre.
Wenn Sie inhaltliche Anmerkungen zu diesem Artikel haben, können Sie die Redaktion per E-Mail informieren. Wir lesen Ihre Zuschrift, bitten jedoch um Verständnis, dass wir nicht jede beantworten können.