Klimaneutralität: Der Umbau der Chemieindustrie
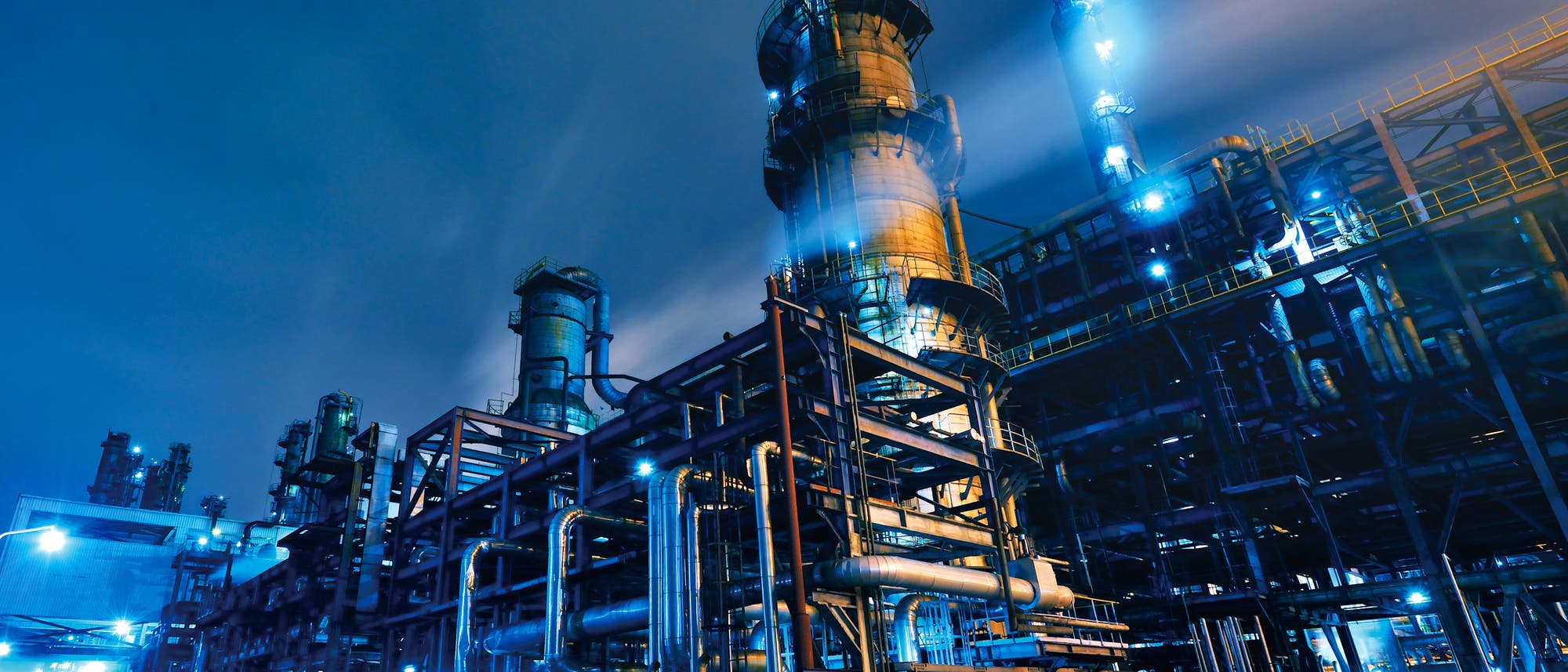
Die Luke öffnet sich. Unmittelbar schlägt Gluthitze mit einem lauten Fauchen heraus, gleißendes Licht sticht in die Augen. Hinter der flimmernden Luft in der Kammer sind auf der rechten Seite rotorange glühende Rohre zu erkennen. Länger als ein paar Sekunden kann man nicht hineinschauen, dann müssen sich Augen, Ohren und Haut kurz erholen.
Luke zu. Es ist wieder sonnig-warm an diesem Junitag in Ludwigshafen, 25 Grad Celsius, fast windstill, im feuerfesten Blaumann nicht gerade erfrischend. Neben uns dröhnt und röhrt die Anlage, von außen fühlt sie sich an wie eine Herdplatte mit Restwärme. Acht Stockwerke hoch erstrecken sich ihre Stahltürme in den blauen Himmel. Meterdicke Rohre führen zu einem weiteren, riesigen runden Turm, dann verzweigt sich alles zu einem Netzwerk verschiedener Kolonnen und Tanks, die in der Ferne mit den zahlreichen anderen Fabriken verschmelzen. Der Steamcracker, so formuliert es der Kollege aus der Pressestelle, sei das Herz der BASF.
Überall auf der Welt stehen solche Anlagen. Stunde um Stunde verwandeln sie eine gelbliche Flüssigkeit, die Chemiker Naphtha nennen, in ein Sortiment kleiner Bausteine, die anschließend als Ausgangsstoffe für etliche Substanzen dienen. Die wichtigsten dieser Bausteine heißen Ethylen und Propylen, Benzol, Toluol und Xylol. Zusammen mit Methanol und Ammoniak bilden sie die sieben Primärchemikalien, auf denen fast die gesamte industrielle organische Chemie basiert: die Substanzen, aus denen Plastiktüten, Zahnpasta, Textilfasern, Waschmittel, Aromen, Dämmstoffe, Medikamente, Flugzeugsitze, Farbpigmente, Treibstoffe und vieles mehr bestehen. Mehrere zigtausend chemische Produkte fabriziert und nutzt die Welt täglich. Rund 70 Prozent der dabei anfallenden CO2-Emissionen entstehen beim Erzeugen der sieben Primärchemikalien.
Bis 2050 soll die Chemieindustrie klimaneutral sein – weltweit, wenn es nach den Zielen des Pariser Klimaschutzabkommens geht. Eine große Aufgabe, denn die Branche belegt nach der Stahl- und der Zementindustrie Platz drei in der Rangliste der größten Kohlenstoffdioxid-Emittenten. 1,4 Milliarden Tonnen waren es weltweit im Jahr 2021, rund vier Prozent der globalen Emissionen.
»Wenn wir den Steamcracker elektrisch beheizen, können wir bis zu 90 Prozent des dort entstehenden CO2 vermeiden«, erzählt Andrea Haunert. Die Ingenieurin leitet bei der BASF die Entwicklung des »eFurnace«, eines komplett elektrisch arbeitenden Steamcracker-Ofens. Gerade hat sie durch den konventionellen Steamcracker geführt und dabei erläutert, was ein »Seitenbrennerofen« ist: An der Seite der Brennkammer, durch welche die Rohre mit dem Dampf-Naphtha-Gemisch führen, sind zahlreiche riesige Gasbrenner nebeneinander angebracht, pro Ofen dreimal 24 Stück. Die überdimensionierten Campingkocher bringen die Kammer auf zirka 1100 Grad. 850 Grad kommen noch in den Rohren an, wo die Spaltung des Naphtha abläuft. Nach rund 60 bis 100 Tagen hat sich an den Innenwänden der Rohre eine dicke Schicht Koks gebildet. Dieses Abfallprodukt wird anschließend wie bei der Pyrolysefunktion eines Backofens mit Hilfe von Dampf und Luft zersetzt. Der Steamcracking-Prozess ist einer der energieintensivsten in der Branche.
Tatsächlich ist die Chemieindustrie der größte Energiekonsument überhaupt. Sie setzt ein ganzes Zehntel der weltweit erzeugten Energie um, mehr als jede andere Industrie. 2021 bezog sie laut der Internationalen Energieagentur (IEA) Prozessenergie von 889 Terawattstunden (TWh) aus Kohle, 1361 TWh aus Erdgas, 194 aus Strom, 28 aus Erdöl. Viele Prozesse sind heute zwar stark optimiert: Wärme, die durch die chemischen Reaktionen entsteht, wird möglichst an anderer Stelle wieder eingesetzt. Dank solcher und anderer Verbesserungen sind die Emissionen seit den 1990er Jahren stark gesunken, wie Vertreter von Chemieunternehmen immer wieder betonen. Doch nun muss sich etwas Grundlegendes ändern, um den CO2-Fußabdruck weiter substanziell zu senken. Einer der großen Hebel ist es, die energiehungrigsten Prozesse mit grünem Strom zu betreiben.
Elektrische Heizung statt Gasbrenner
Die Fachleute in Ludwigshafen erproben im Zuge des Projekts eFurnace zwei Möglichkeiten, um die Hitze für den Steamcracker elektrisch zu erzeugen. Die erste, die indirekte Heizung, funktioniert ähnlich wie die konventionelle: Mit Hilfe von elektrischem Strom wird eine Kammer rund um den Reaktionsbereich der Rohre aufgeheizt. Das Gemisch darin erhält seine Temperatur durch Wärmestrahlung. Bei der zweiten, direkten Methode hingegen fließt der elektrische Strom unmittelbar durch die Rohre und erzeugt genau dort durch elektrischen Widerstand die nötige Hitze. Die stromführenden Rohre neu zu entwickeln und so mit der Stromquelle zu verbinden, dass es funktioniert, sei der Knackpunkt gewesen, berichtet Haunert. Wie sie das Problem gelöst haben, ist jedoch ein Firmengeheimnis. Für das Projekt eFurnace hat sich die BASF mit dem Anlagenbauer Linde und der saudi-arabischen Chemiefirma Sabic zusammengetan. Alle gemeinsamen Entwicklungen werden gemeinsam patentiert.
Welche Methode besser funktioniert, wird sich bald zeigen. Bislang stehen der kleine, dicke und der große, dünne Stahlturm still nebeneinander hinter einem Bauzaun. Im April 2024 wird die Pilotanlage ihren Betrieb starten und dann drei Jahre lang laufen. Zunächst sollen die Öfen etwa vier Tonnen Naphtha pro Stunde verarbeiten. Von der späteren Auslegung sei das gar nicht so weit entfernt, ordnet Haunert ein: Eine Skalierung auf die zehnfache Größe wäre ausreichend für den Ersatz eines konventionellen Ofens. Denn in derzeit aktiven Steamcrackern arbeiten typischerweise sechs bis zehn Öfen parallel. Ist das Konzept erfolgreich, lassen sich bestehende Anlagen also im besten Fall schrittweise umrüsten.
»Man kann ziemlich viel CO2 einsparen, wenn man Steamcracker durch elektrischen Strom beheizt statt wie bislang durch die Verfeuerung von Erdgas«, sagt auch Kurt Wagemann. Der Chemiker war von 2010 bis 2021 Geschäftsführer der DECHEMA – Gesellschaft für chemische Technik und Biotechnologie. Trotzdem ist die Umrüstung für ihn erst der Anfang: »Die Frage ist: Was ist der Rohstoff? Bislang ist das Naphtha, ein Nebenprodukt aus der Kraftstoffproduktion. Wenn wir einen Schritt weitergehen und fragen, wie man noch mehr CO2 einsparen kann, dann wird man einen Rohstoffwechsel vollziehen.«
Um in einer Welt ohne fossile Ressourcen zu bestehen, muss sich die chemische Industrie also nicht nur neue Energieträger, sondern auch neue Bausubstanzen suchen. »Wir brauchen Kohlenstoff«, bringt es Andrea Haunert auf den Punkt. Egal, ob Plastiktüte, Ibuprofen-Tablette, Waschmittel oder Anstrichfarbe – alle petrochemischen Produkte besitzen ein Grundgerüst aus Kohlenstoffatomen, die bislang günstig aus Erdöl und Erdgas zu erhalten waren. Künftig könnten Biomasse, Kunststoffabfälle und CO2 die neue Rohstoffbasis bilden. Sie alle enthalten Kohlenstoff, doch um ihn verwertbar zu machen, bedarf es anderer Mittel als jener, die bereits etabliert sind.
»CHx ist quasi die Formel für die fossilen Rohstoffe, denn die bestehen nur aus Kohlenstoff (C) und Wasserstoff (H). Die anderen Elemente bauen wir dann ein«, veranschaulicht Walter Leitner, Katalyseforscher und Direktor am Max-Planck-Institut für chemische Energiekonversion CEC, die traditionelle Denkweise. Er hat sich darauf spezialisiert, das notorisch reaktionsträge CO2 zur Reaktion zu bringen, um wieder nützliche Substanzen daraus herzustellen. CO2 ist aus chemischer Sicht eigentlich ein Endprodukt: Es entsteht, wenn kohlenstoffhaltiges Material zersetzt wird oder verbrennt. Nutzt man es wieder als Ausgangsstoff, um neue Stoffe herzustellen, schafft man einen Kreislauf, was Ressourcen spart und Emissionen vermeidet. Es ist aber nicht ganz trivial. Zum einen besteht die Kunst darin, das Molekül aus seinem energetischen Tief heraus zu aktivieren, was mit Hilfe geeigneter Katalysatoren gelingt. Zum anderen benötigt man, um aus CO2 wieder einen nützlichen Baustein herzustellen, Wasserstoff. Und klimaneutral hergestellter Wasserstoff ist bislang noch ein äußerst knappes Gut.
Schon heute verbraucht die chemische Industrie weltweit rund die Hälfte des leichten Gases, 2022 waren es 46 von 94 Millionen erzeugten Tonnen. Es dient hauptsächlich dazu, Methanol und Ammoniak herzustellen, zwei der am meisten produzierten Chemikalien überhaupt. Methanol (CH3OH) bildet die Ausgangsbasis für eine breite Palette an Produkten, drei Viertel des hergestellten Ammoniaks (NH3) werden zu Dünger weiterverarbeitet.
Aus Wasserstoff und CO2 ließe sich Synthesegas erzeugen, ein Gemisch aus Kohlenstoffmonoxid und Wasserstoff. Synthesegas ist eine universelle Basis, um verschiedenste Kohlenwasserstoffe herzustellen. Dann bieten sich zwei Wege an: Man könnte daraus eine Art künstliches Naphtha herstellen und dieses wiederum im Steamcracker zu den üblichen Produkten umsetzen. Oder Methanol erzeugen und die klassischen »Crackerprodukte« auf alternativen Routen herstellen.
Der zusätzliche Wasserstoffhunger wäre enorm. In einer im März 2023 veröffentlichten Studie haben der Verband der Chemischen Industrie (VCI) und der Verein Deutscher Ingenieure (VDI) drei verschiedene Szenarien untersucht, wie die chemische Industrie in Deutschland bis 2045 treibhausgasneutral werden kann. Die Experten haben Rohstoff- und Energiebedarf akribisch ermittelt. Demnach erzeugt und verbraucht die hiesige Chemieindustrie derzeit 1045 Kilotonnen Wasserstoff im Jahr. Hinzu kommen – je nachdem, ob man Grundstoffe künftig aus Methanol oder künstlichem Naphtha herstellt – zwischen 6998 und 5775 Kilotonnen, dazu 627 Kilotonnen H2 als Brennstoff für Hochtemperaturprozesse, die sich nicht elektrisch in Gang setzen lassen. Insgesamt sind also zwischen 7447 und 8670 Kilotonnen emissionsfreier Wasserstoff nötig. Die bereits vorhandenen Wasserstoffkapazitäten werden nicht mitgezählt, denn sie müssen komplett ersetzt werden: Die Wasserstoffproduktion, wie sie heute betrieben wird, ist einer der emissionsreichsten Prozesse in der gesamten Chemie. Elektrolyseanlagen, die Wasser mit Hilfe von grünem Strom spalten und das begehrte Gas klimaneutral erzeugen, findet man bislang nur sporadisch.
Derzeit laufen viele Projekte nicht an, weil grüner Wasserstoff fehlt
Deshalb laufen Projekte wie Methanolanlagen auf Basis von CO2 und H2 noch nicht in großem Stil an. »Es gibt die Katalysatoren und die Verfahren dazu. Woran es mangelt, ist emissionsfrei hergestellter Wasserstoff«, sagt auch Lars Kissau, der bei der BASF für das Erreichen der Netto-Null-Ziele bis 2050 verantwortlich ist. »Diese Technologie ergibt nur Sinn, wenn emissionsfreier Wasserstoff in ausreichender Menge zur Verfügung steht.« Das gehe nicht von heute auf morgen, gibt Kurt Wagemann von der DECHEMA zu bedenken. »Die Zahl der Elektrolyseure nimmt zu, genau wie die Zahl der Ideen, grünen Wasserstoff mit Hilfe von Fotovoltaik oder Windkraft an günstigen Standorten zu produzieren«, urteilt der Experte. In Südchile betreiben Porsche und Siemens einen mit Strom aus Windkraft betriebenen Elektrolyseur, Deutschland baut Wasserstoffpartnerschaften mit Namibia oder Saudi-Arabien aus. Die DECHEMA plädiert allerdings dafür, solche Standorte auch innerhalb Europas aufzubauen und einen großen Teil des benötigten Wasserstoffs in Deutschland oder Europa herzustellen. »Wenn Wasserstoff woanders günstig produziert wird, dann kann vor Ort schnell die Idee aufkommen, auch den Folgeschritt zu etablieren und direkt Methanol oder Ammoniak herzustellen«, führt Wagemann aus. Das könnte die hier ansässige Grundstoffindustrie direkt gefährden. Um sie hier zu halten, sei es demnach wichtig, günstigen »grünen« Strom in Deutschland und der EU bereitzustellen, damit der Wasserstoff direkt auch hier produziert werden kann.
Auf dem BASF-Werk in Ludwigshafen liefern derzeit drei Gaskraftwerke mehr als fünf Terawattstunden (TWh) Strom im Jahr, damit ist der Standort rechnerisch energieautark. »Wenn wir Prozesse elektrifizieren, die bisher auf fossilen Brennstoffen basieren, werden wir an großen Standorten wie Ludwigshafen doppelt bis dreimal so viel Strom benötigen wie heute«, prognostiziert Kissau. Und dieser Strom soll nach Möglichkeit aus erneuerbaren Quellen stammen. Anfang 2022 hat die BASF daher die Tochterfirma BASF Renewable Energy GmbH gegründet, die durch langfristige Lieferverträge große Mengen erneuerbarer Energie beschafft oder für die Versorgung der Werke mit Strom direkt in Wind- und Solarparks investiert. So entsteht beispielsweise vor der holländischen Küste einer der weltweit größten Offshore-Windparks mit 1,5 Gigawatt Leistung. Neben dem Chemiekonzern sind der Energielieferant Vattenfall und der Versicherer Allianz an dem Projekt beteiligt, die BASF erhält knapp die Hälfte des dort erzeugten Stroms. Der Windpark wurde 2023 eingeweiht und soll 2024 betriebsbereit sein.
Wolle man die ganze fossile Rohstoffbasis durch CO2 ersetzen, benötige die deutsche Chemieindustrie im Jahr 2045 zwischen 464 und 508 TWh Strom, rechnen VDI und VCI in ihrer Studie vor. Zum Vergleich: 2021 verbrauchte sie gemeinsam mit der Pharmabranche insgesamt rund 224 TWh Energie, also weniger als die Hälfte. Und davon deckte sie knapp ein Viertel – 53 TWh – durch Strom, was rund 10 Prozent des bundesweiten Verbrauchs entsprach.
Ist das ganze Vorhaben also ein Ding der Unmöglichkeit? Walter Leitner erinnert daran, dass es nicht gleich einen vollständigen Umbau braucht, um etwas zu verändern. »Es gibt Fälle, bei denen CO2 heute schon ein günstigerer Rohstoff sein kann, selbst unter fossiler Energieversorgung«, berichtet er. Etwa, weil andere Chemikalien eingesetzt werden oder der neue Syntheseweg »eleganter« ist, das heißt weniger Schritte beinhaltet und weniger Ressourcen verbraucht. »Wir forschen intensiv an Technologien für großskalige Lösungen wie etwa Methanol aus CO2, die sozusagen an der Wurzel der chemischen Wertschöpfung ansetzen. Gleichzeitig arbeiten wir stark daran, neue Wege zu ermöglichen – damit wir nicht warten müssen, bis das Energiesystem umgestellt ist, sondern vielmehr die Transformation beschleunigen«, erzählt der Chemiker weiter. Leitner hat Wege gefunden, CO2 in speziellere Stoffe wie Ameisensäure oder organische Karbonate umzuwandeln, die wiederum zu neuartigen Kunststoffen umgesetzt werden. Solche Moleküle lassen sich in den »Wertschöpfungsbaum« der Chemie einbauen. Zwar werden diese in viel kleineren Mengen produziert als Grundchemikalien wie Methanol, und entsprechend betrifft eine verbesserte CO2-Bilanz einen überschaubaren Teil der Chemie. Doch »weil diese Stoffe vom Erdöl aus gesehen schon einige Herstellungsschritte beinhalten, haben sie bereits einen recht großen CO2-Rucksack«, veranschaulicht der Chemiker. Daher könne man durch solche Neuerungen rasch und mit weniger Energieaufwand eine Verbesserung erreichen.
Nebenbei entstehen so alternative Materialien, die wiederum Chancen eröffnen, wie Leitner erwähnt. So seien schon Polymere entwickelt worden, die sich leichter durch chemisches Recycling in ihre Bestandteile zurück spalten lassen als ihre herkömmlichen Pendants, oder synthetische Kraftstoffe, die bei der Verbrennung geringere Mengen an schädlichen Stickoxiden ausstoßen.
Die Studie von VCI und VDI nimmt aber noch ein drittes Szenario unter die Lupe: eines, bei dem man möglichst viel Kohlenstoff aus Kunststoffabfällen und Biomasse gewinnt. Dann würde der Bedarf auf 325 TWh Strom sinken, und man bräuchte bloß Wasserstoff mit einem Energiewert von 148 TWh im Jahr 2045.
Kunststoffabfälle lassen sich entweder mechanisch recyceln, durch chemische Prozesse in ihre Grundbausteine zerlegen – oder bei hohen Temperaturen unter Luftausschluss pyrolysieren. So erhält man wieder eine dem Naphtha ähnliche Substanz, die genau wie ihr fossiles Pendant in den Steamcracker gefüttert werden kann. Letztere Option favorisiere die chemische Industrie weltweit, sagt Wagemann. »Daran wird intensiv gearbeitet. Das ist die einfachste Variante für gemischte Kunststoffe.« Teilweise geschieht das bereits, auch die BASF setzt rezyklierte Kunststoffe als Grundstoff ein, jedoch bislang auf Kundenwunsch und in kleinen Mengen.
Eine weitere mögliche Kohlenstoffquelle ist Biomasse – also im besten Fall Pflanzenmaterial, das sich nicht für Nahrungsmittel verwenden lässt. Selbst das könnte man durch Pyrolyse in eine Art Bio-Naphtha verwandeln, oder durch Gasifizierung in eine Art Synthesegas. Das stößt aber längst nicht bei allen Experten auf Zustimmung. »Mir blutet ein wenig das Herz angesichts solcher Ansätze«, sagt Christine Rasche, die am Fraunhofer-Institut für Grenzflächen- und Bioverfahrenstechnik IGB in Leuna das Geschäftsfeld »Nachhaltige Chemie« leitet. Sie plädiert dafür, die wertvollen Strukturen zu nutzen, die von den Pflanzen bereits aufgebaut wurden. »Wir haben hier eine einzigartige Syntheseleistung der Natur«, betont sie.
Strukturen von Lignocellulose nutzen
In Leuna steht seit 2012 die Lignocellulose-Bioraffinerie, eine Pilotanlage, die täglich bis zu 70 Kilogramm Trockenmasse von Holzhackschnitzeln, Stroh oder anderem Biomaterial verarbeiten kann. Solche holzigen Pflanzen bestehen zum Großteil aus Lignocellulose, einem höchst komplexen Biopolymer. Anders als Polymere aus konventionellen Kunststoffen besitzt es nicht bloß Ketten von zwei oder drei sich immer wiederholenden Bausteinen, sondern stützt sich auf drei verschiedene, teils miteinander verbundene Strukturelemente. Das ist erstens Zellulose, eine lange Kette von Zuckern, die auch den Hauptbestandteil von Pflanzenstielen und -blättern bildet – oder von Papier. Zweitens Hemicellulose, ein verzweigtes Polymer aus anderen Zuckern. Und schließlich Lignin, ein Verbund verschiedener Aromaten mit unterschiedlicher Zusammensetzung je nach Pflanzensorte.
»Lignin bringt aromatische Strukturen und spezifische Funktionalitäten mit. Davon sind viele sehr interessant für viele Materialien, die wir ersetzen müssen«, erläutert Rasche. Lange galt Lignocellulose, vor allem das enthaltene Lignin, jedoch als zu schwierig für eine weitere Nutzung. In der Papierindustrie fällt es als Abfall an und wird verbrannt, um Prozessenergie zu liefern. Doch es lohne sich, Wege zu finden, die Strukturen des Lignins zu nutzen, findet auch Wagemann: »Es ist sicher komplizierter, aber man sollte sich immer bemühen, das, was schon an Aufbauleistung drinsteckt, möglichst weitgehend wieder nutzbar zu machen.«
Die Wissenschaftlerinnen und Wissenschaftler am Fraunhofer IGB haben ein Verfahren zur Auftrennung von Lignocellulose aus den 1930er Jahren in den Pilotmaßstab überführt und die Methode effizienter und wirtschaftlicher gemacht, so dass sie praxistauglich ist. Auch das Max-Planck-Institut für Dynamik komplexer technischer Systeme war beteiligt, um einen Weg zu finden, speziell Lignin von den weiteren Bestandteilen zu isolieren. Holzhackschnitzel oder anderes Biomaterial wird dazu mit einer Mischung aus Ethanol und Wasser bei hohem Druck und hoher Temperatur »gekocht«, dann werden Zellulose, Hemicellulose und Lignin durch verschiedene Fällungs- oder Trennverfahren separiert. Zellulose kann danach in Zuckermoleküle gespalten werden, die Bakterien oder Enzyme anschließend in Bioreaktoren umsetzen, beispielsweise zu Ethanol. Die Hemicellulose-Moleküle lassen sich ebenfalls in ihre Zuckerbestandteile auftrennen und fermentativ weiterverarbeiten.
Die Bausteine des Lignins sind Phenolderivate, aus denen sich bei der Spaltung des Polymers die Phenole Guajakol, Catechol, Vanillin, Syringol und Phenol gewinnen lassen. Deren aromatisches Grundgerüst ist für zahlreiche chemische Stoffe zentral, man braucht es etwa für Medikamente, Pestizide oder Aromastoffe. In der klassischen Synthese nutzt man für deren Aufbau die aus dem Steamcracker erhaltenen Aromaten Benzol, Toluol und Xylol. »Es gab anfangs Bestrebungen, aus Lignin tatsächlich Lösemittel wie Benzol oder Phenol herzustellen«, erzählt die Lebensmittelchemikerin Rasche. Die Leunaer Fachleute sind davon allerdings abgekommen, denn es hat sich als sehr aufwändig erwiesen, die aromatischen Monomere – also Einzelmoleküle – aus Lignin zu gewinnen. Zu große Mengen an Lösungsmitteln und zu viel Energie braucht es, um substanzielle Mengen davon zu erhalten. »Interessanter ist es zu schauen, wo solche Phenole angewandt werden«, erklärt Rasche. Das sind oft Phenolharze, Beschichtungen oder Polyurethanschäume. Häufig reiche es für diese Zwecke aus, Lignin in Oligomere zu spalten, das sind zwei bis zehn miteinander verbundene Monomere. Mitunter lässt sich sogar das intakte Polymer nutzen. »Man muss dann schauen, welche intrinsischen Eigenschaften des Lignins nützlich sind, etwa der mitgebrachte UV-Schutz«, gibt Rasche ein Beispiel.
Möglicherweise sind solche speziellen Anwendungen genau das Richtige für die Nutzung von Biomasse, gerade weil sie nicht im Überfluss verfügbar ist. »Wir haben begrenzte Flächen, die ja auch eine ökologische Bedeutung haben, etwa für die Biodiversität. Man kann nicht beliebig Rohstoffe aus der Natur ziehen«, merkt Wagemann an. In Sachen Rohstoffverfügbarkeit haben VDI und VCI aber auch hinsichtlich der Kunststoffe eine ernüchternde Nachricht: Nur sechs Prozent der »high-value chemicals« – der Olefine und Aromaten aus dem Steamcracker – ließen sich künftig auf Basis recycelten Plastiks herstellen. Für mehr reicht es nicht, denn von den Kunststoffen, die jedes Jahr in wachsenden Mengen produziert werden, wird nur wenig recycelt. Der größte Teil landet in Deponien oder Meeren, ein ebenfalls großer Part wird verbrannt. »Es steht also nicht so viel zur Verfügung, wie man gern hätte,« schließt Wagemann.
Knappes CO2?
Ironischerweise könnte mittelfristig auch das CO2 knapp werden. Die Emissionen eines fahrenden Autos kann die chemische Industrie nicht auffangen, ebenso wenig die von Gebäudeheizungen oder anderen verteilten Quellen. In Zukunft bleiben für Chemiewerke daher schwer vermeidbare Restemissionen aus anderen Industrien oder das direkte Abtrennen aus der Luft (direct air capture, DAC). »Die chemische Industrie spekuliert auf den Rohstoff CO2 aus der Zement- und Kalkindustrie«, verrät Branchenexperte Wagemann, außerdem auf dasjenige aus Biogasanlagen, biotechnologischen Fermentationsanlagen sowie der Abfallverbrennung.
Leitner warnt gleichzeitig davor, das Auffangen und Nutzen von Kohlenstoffdioxid (carbon capture and utilization, CCU) als bequeme Emissionsminderung zu sehen. »Man sollte die CO2-Nutzung nicht als einen Weg betrachten, um die fossile Welt weiter zu erhalten und das CO2, das dabei entsteht, in Chemieprodukte umzuwandeln. Es ist kein Weg, das Gas loszuwerden, sondern der notwendige Weg, um von fossilen Rohstoffen loszukommen.«
Wenn Sie inhaltliche Anmerkungen zu diesem Artikel haben, können Sie die Redaktion per E-Mail informieren. Wir lesen Ihre Zuschrift, bitten jedoch um Verständnis, dass wir nicht jede beantworten können.