Rohstoffe: Wasserstoff macht Biomasse zu hochwertigen Chemikalien
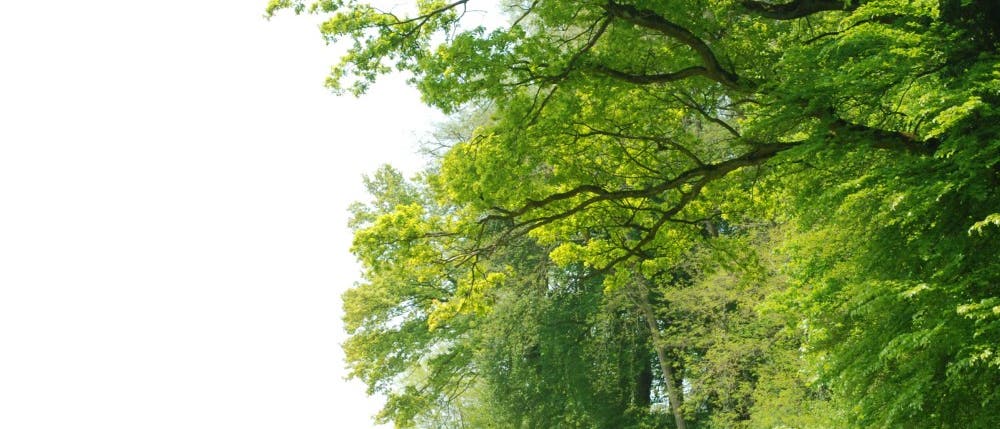
© Richard Zinken (Ausschnitt)
Wissenschaftler haben einen Weg gefunden, dreimal so viele Grundchemikalien aus Biomasse zu produzieren wie bisher möglich. Dazu setzen die Forscher um George Huber von der University of Massachusetts ein thermisches Zersetzungsprodukt von Biomasse, das Pyrolyseöl, mit Wasserstoff und zwei Metallkatalysatoren um, bevor sie es an einem weiteren Katalysator zu den gewünschten Kohlenwasserstoffen reagieren lassen. Etwa 70 Prozent des Kohlenstoffs der Ausgangsprodukte können so in nutzbare Chemikalien umgewandelt werden.
Der Prozess basiert auf dem lange bekannten Verfahren der Pyrolyse. Unter Sauerstoffausschluss zerlegen Temperaturen um 500 Grad die Makromoleküle in ein braun-schwarzes Gemisch aus verschiedenen organischen Stoffen, das man als Pyrolyseöl bezeichnet und das sich als kostengünstiger und leicht verfügbarer Ersatz für Erdöl als Quelle wichtiger Industriechemikalien anbietet. Allerdings enthalten die Verbindungen als Erbe ihrer biologischen Herkunft einen hohen Anteil Sauerstoff: Das Pyrolyseöl enthält Zucker, Ketone, organische Säuren und mehrwertige Alkohole, während die chemische Industrie nach Aromaten, Olefinen und anderen Kohlenwasserstoffen verlangt.
Bisherige Verfahren, Pyrolyseöle zu veredeln, also ihnen einen Teil ihres Sauerstoffs zu entziehen, nutzen Zeolithe, poröse anorganische Festkörper mit katalytischen Eigenschaften. Die Produkte der direkten Pyrolyse sind jedoch gegenüber hohen Temperaturen oft sehr instabil, so dass statt nützlicher Chemikalien nur ein kohliger Rückstand bleibt, vergleichbar mit Zucker, der auf einer Herdplatte verschmurgelt.
Das Team um Gruber löste dieses Problem, indem es die empfindlichen Verbindungen in der Flüssigkeit mit Wasserstoff reagieren ließ, zuerst an fein verteiltem Ruthenium bei 100 Grad, anschließend an Platin bei 500 Grad. Dabei verlieren die Verbindungen einen Teil ihres Sauerstoffgehalts und damit auch die Neigung, im Zeolithkatalysator zu karamellisieren. Bis zu 70 Prozent des Kohlenstoffs konnten sie so in die begehrten Rohstoffe umsetzen, aus denen unter anderem Kunststoffe oder Medikamente entstehen.
Durch Kontrolle der genauen Prozessbedingungen lasse sich die Zusammensetzung des Produkts präzise an den Bedarf anpassen, schreiben die beteiligten Forscher. Sie haben bereits ein Unternehmen gegründet, das das neue Verfahren kommerziell in industriellem Maßstab umsetzen soll. (lf)
Der Prozess basiert auf dem lange bekannten Verfahren der Pyrolyse. Unter Sauerstoffausschluss zerlegen Temperaturen um 500 Grad die Makromoleküle in ein braun-schwarzes Gemisch aus verschiedenen organischen Stoffen, das man als Pyrolyseöl bezeichnet und das sich als kostengünstiger und leicht verfügbarer Ersatz für Erdöl als Quelle wichtiger Industriechemikalien anbietet. Allerdings enthalten die Verbindungen als Erbe ihrer biologischen Herkunft einen hohen Anteil Sauerstoff: Das Pyrolyseöl enthält Zucker, Ketone, organische Säuren und mehrwertige Alkohole, während die chemische Industrie nach Aromaten, Olefinen und anderen Kohlenwasserstoffen verlangt.
Bisherige Verfahren, Pyrolyseöle zu veredeln, also ihnen einen Teil ihres Sauerstoffs zu entziehen, nutzen Zeolithe, poröse anorganische Festkörper mit katalytischen Eigenschaften. Die Produkte der direkten Pyrolyse sind jedoch gegenüber hohen Temperaturen oft sehr instabil, so dass statt nützlicher Chemikalien nur ein kohliger Rückstand bleibt, vergleichbar mit Zucker, der auf einer Herdplatte verschmurgelt.
Das Team um Gruber löste dieses Problem, indem es die empfindlichen Verbindungen in der Flüssigkeit mit Wasserstoff reagieren ließ, zuerst an fein verteiltem Ruthenium bei 100 Grad, anschließend an Platin bei 500 Grad. Dabei verlieren die Verbindungen einen Teil ihres Sauerstoffgehalts und damit auch die Neigung, im Zeolithkatalysator zu karamellisieren. Bis zu 70 Prozent des Kohlenstoffs konnten sie so in die begehrten Rohstoffe umsetzen, aus denen unter anderem Kunststoffe oder Medikamente entstehen.
Durch Kontrolle der genauen Prozessbedingungen lasse sich die Zusammensetzung des Produkts präzise an den Bedarf anpassen, schreiben die beteiligten Forscher. Sie haben bereits ein Unternehmen gegründet, das das neue Verfahren kommerziell in industriellem Maßstab umsetzen soll. (lf)
Schreiben Sie uns!
Beitrag schreiben