Digitales Bauen: Das Haus aus der Spritzdüse
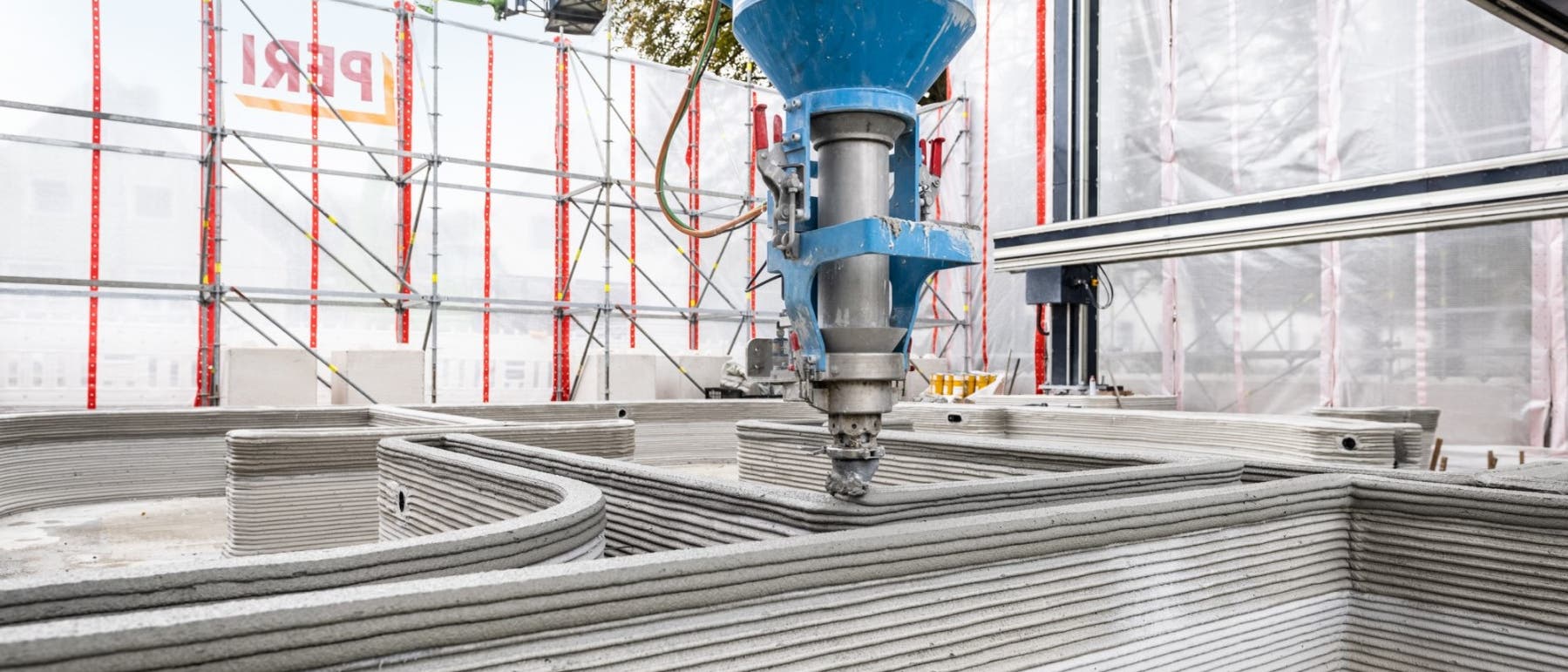
Europas größtes 3-D-gedrucktes Gebäude ist 54 Meter lang, neun Meter hoch und steht in Heidelberg. Der wellenförmige Gewerbebau »Wave House« wurde in rund 170 Druckstunden errichtet und Ende Januar 2024 als Rechenzentrum eingeweiht. Er zeigt den Beginn einer tief greifenden Veränderung im Bauwesen. Ein 3-D-gedrucktes Haus wird am Computer entworfen und auch vom Computer gesteuert gebaut. Das Verfahren ermöglicht zugleich eine große gestalterische Freiheit, gerade in Bezug auf Rundungen, was wiederum den Materialeinsatz reduziert. Und weniger Material bedeutet geringere Kosten und weniger Treibhausgasemissionen.
Das Material, oft Beton, kommt aus einer Spritzdüse am Ende eines Roboterarms, was so ähnlich aussieht, als würde man Zahnpasta aus einer Riesentube drücken. Allerdings legt die Maschine die Materialstränge übereinander, so dass Schicht um Schicht zum Beispiel eine Hauswand entsteht. Die Öffnungen für geplante Türen, Fenster, Versorgungsschächte und Steckdosen spart der Roboter aus. Das Spritzverfahren verleiht den Bauteilen eine charakteristische Riffeloptik.
Für das Wave House lieferte die Firma Heidelberg Materials mehr als 300 Tonnen eines eigens entwickelten 3-D-Druckbetons. »Das dabei eingesetzte Bindemittel senkt den CO2-Ausstoß um 55 Prozent gegenüber dem sonst üblichen Portlandzement«, sagt Jörg Dietrich, Leiter Engineering & Innovation und Leiter Produktmanagement bei Heidelberg Materials Deutschland. Außerdem sei der mineralische 3-D-Druckbeton »zu hundert Prozent recycelbar«, das heißt, die Gebäudeteile könnten später einmal abgerissen und gebrochen und das Material wiederverwertet werden.
Emissionsarm, Ressourcen schonend und kostengünstiger
Zum Beispiel kann man das Recyclingmaterial als Rohstoff für die Zementproduktion verwenden. »Die Wiederverwertung von Beton und Zement auf gleicher Qualitätsebene treiben wir aktuell massiv voran«, sagt Dietrich. Das Baustoffunternehmen lieferte bereits im Herbst 2020 das Material für das erste 3-D-gedruckte Wohnhaus in Deutschland und stellt nun auch den Baustoff für ein öffentlich gefördertes Mehrfamilienhaus im nordrhein-westfälischen Lünen her. Dank der guten Erfahrungen ist Dietrich vom Potenzial dieser Technologie überzeugt. »Dabei stehen wir ja erst am Anfang einer Entwicklung, in der es noch viel zu lernen und auszuprobieren gibt.«
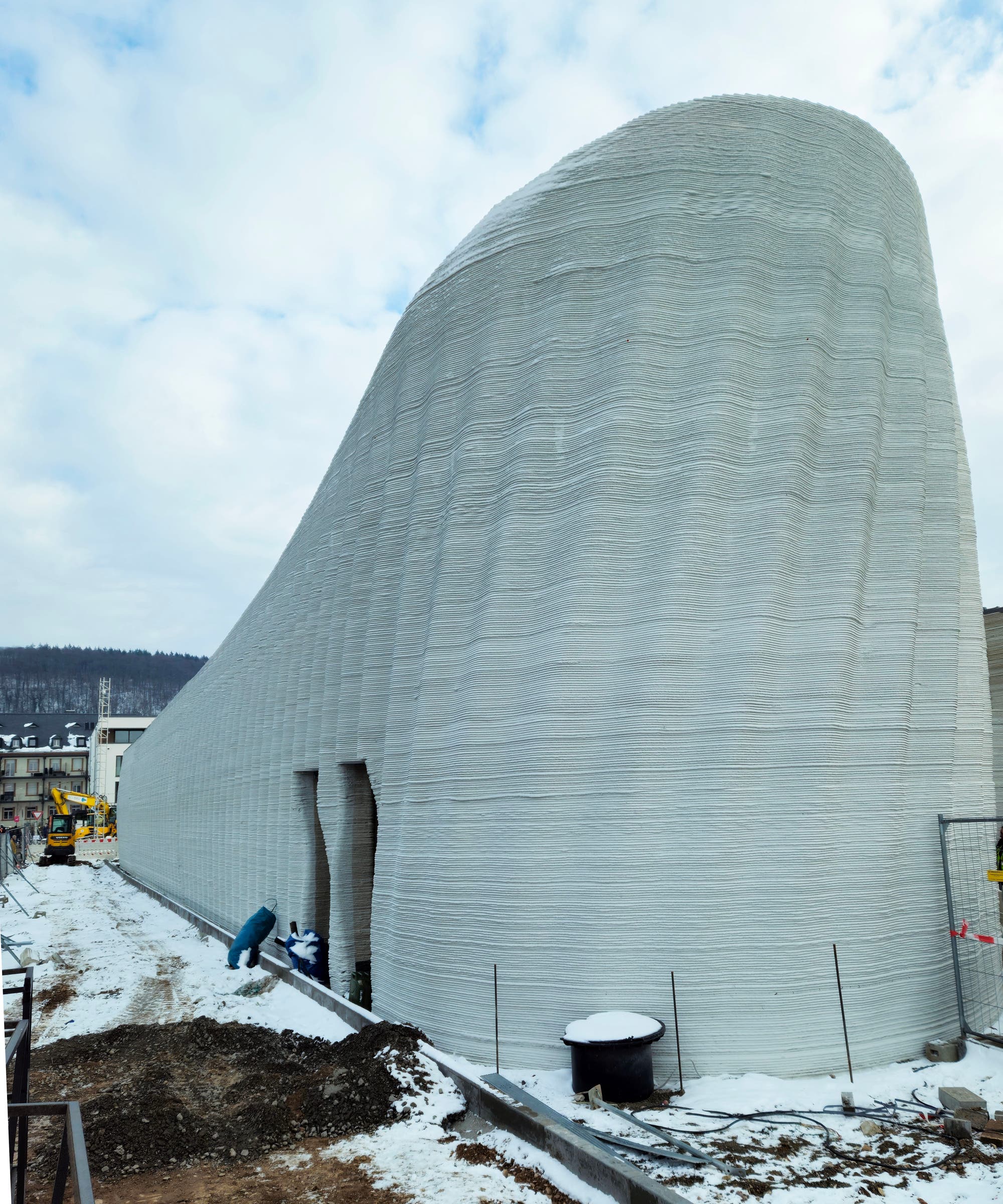
So ist ein Ziel, die Rezepturen des Materials und des Bindemittels weiterzuentwickeln, damit die Emissionen weiter sinken. Nicht nur Heidelberg Materials will und muss in Zukunft klimaneutral werden, das gilt für die Branche insgesamt. 3-D-Druck ist ein Trittstein auf dem Weg dahin. »Der 3-D-Druck wird sich bewähren«, bestätigt Jörg Dietrich. »Das heißt aber nicht, dass in zehn Jahren alle neuen Gebäude aus dem Drucker kommen.«
Rund 40 Prozent der weltweiten CO2-Emissionen stammen aus dem Bausektor. Hinzu kommen laut Daten des Exzellenzclusters IntCDC der Universität Stuttgart 40 Prozent des Energie- und Ressourcenverbrauchs sowie 50 Prozent der globalen Müllmenge. Zugleich besteht ein enormer Bedarf an Wohnungen, nicht nur in Deutschland, sondern weltweit. Um diesen Bedarf zu decken und gleichzeitig das Klima zu schützen, ist ein Umdenken im Bauwesen erforderlich.
Der automatisierte Hausbau mit Hilfe eines Roboters bietet dabei eine Reihe von Vorteilen: 3-D-Druck macht laut Fachleuten nicht nur den Materialeinsatz effizienter, er verkürzt auch die Bauzeit und reduziert den Personalbedarf auf einer Baustelle. Angesichts des herrschenden Fachkräftemangels, vor allem im Handwerk, ist das ein großer Bonus – und senkt die Kosten nochmals. Deswegen lenken sowohl Unternehmen als auch Forschungseinrichtungen ihr Augenmerk verstärkt auf die Technik.
3-D-Druck verändert auch die Planung
Wie sich digitale Fertigungstechnologien unter realen Bedingungen auf Planungs- und Produktionsprozesse auswirken, erforscht beispielsweise ein Team an der TU Braunschweig im Projekt »Die digitale Baustelle – Bauindustrie 4.0 als Schlüssel für eine digitale und nachhaltige Bauwirtschaft«. Im Zentrum der Forschungsanlage steht ein sechs Meter hoher 3-D-Drucker, mit dem große Bauteile Energie und Ressourcen schonend hergestellt werden können. Weitere digital gesteuerte Großgeräte wie mobile Roboter und eine automatisierte Betonmischanlage gehören ebenfalls zur Baustelle am Uni-Campus Braunschweig. »Additive Fertigungsmethoden und der 3-D-Betondruck sind Schlüsseltechnologien für den Wandel der Bauwirtschaft«, sagt Patrick Schwerdtner, Mitinitiator der digitalen Baustelle und Professor am Institut für Bauwirtschaft und Baubetrieb laut einer Mitteilung. »Sie vereinen Ökonomie, Ökologie und soziale Aspekte der Bauproduktion.«
»Wir stehen ja erst am Anfang einer Entwicklung, in der es noch viel zu lernen und auszuprobieren gibt«Jörg Dietrich, Heidelberg Materials Deutschland
Weil man bei der Drucktechnik auf die Schalung – die Gussform für Frischbeton – verzichten könne, falle nicht nur ein kostenintensiver Arbeitsgang weg, erklärt Schwerdtner, Projektleiter für Planung und Beschaffung. Die additive Fertigung spare außerdem Material, sagt er. Bei der Technik trägt man Beton nur dort auf, wo er aus Gründen der Konstruktion benötigt wird. Die automatisierte Bauweise erhöhe zudem die Arbeitssicherheit, weil die Bauteile nicht mehr von Handwerkern hergestellt werden, die teilweise unter schwierigen lokalen Bedingungen und bei schlechtem Wetter arbeiten müssten.
Im Maßstab 1 : 1 erproben die Fachleute der TU Braunschweig gemeinsam mit den Kollegen von der TU München auf der digitalen Baustelle außerdem die Vernetzung der additiven Technologien sowie neue Wege der Qualitätskontrolle mit Hilfe von automatischer 3-D-Vermessung. Ziel sei eine durchgehend datenbasierte Arbeit auf der Baustelle, wodurch letztlich auch Fehler in der Kommunikation vermieden würden. Beispielsweise verbindet die digital gesteuerte Betonmischanlage für den 3-D-Druck Arbeitsgänge, die sonst getrennt voneinander ablaufen: etwa das Vermengen der Ausgangsstoffe, um den Beton herzustellen, seine Förderung durch Pumpen und die Kontrolle seiner Eigenschaften wie beispielsweise der Fließfähigkeit. All dies wird in einem digital durchgängigen Prozess gesteuert.
3-D-Druck mit Flachs oder Hanf
Dank solcher Drucktechniken mit weniger Energie, Rohstoffen und Treibhausgasemissionen zu bauen, ist auch das Ziel anderer Forschungsgruppen. Eine Bewegung für nachhaltiges Bauen gibt es in der Architektur schon lange. Inzwischen nutzt sie ebenfalls digitale Verfahren – in Kombination mit nachwachsenden Rohstoffen. Daran arbeiten etwa die Architekten, Ingenieure und Biologen zweier Exzellenzcluster an den Universitäten Stuttgart und Freiburg interdisziplinär zusammen.
Wie 3-D-Druck mit Naturfasern funktioniert, zum Beispiel mit Flachs, Stroh oder Hanf, ist eines der Forschungsgebiete der deutsch-ägyptischen Architektin Hanaa Dahy, die sich für einen Bottom-up-Ansatz ausspricht: »Erst untersuchen, welches schnell wachsende Material in der Region vorhanden ist. Dann überlegen, was und in welcher Form damit gebaut werden kann.« Für robotergestützte und digitale Fertigungstechniken wählt die assoziierte Professorin für nachhaltiges Design und integrierte Technologie an der Universität Aalborg in Kopenhagen bevorzugt schnell wachsende Rohstoffe – und kein Holz. Es sei denn, es handelt sich um »Abfälle« von Sägewerken, etwa Holzpulver, das man als Füllstoff zusammen mit Biokunststoffen verwenden kann.
Dass sich auch mit Pflanzenfasern aus Flachs in Kombination mit 3-D-Fertigung eine erstaunliche Tragkraft erzielen lässt, zeigen drei Stadtbrücken für Fußgänger und Radfahrer. Sie entstanden im Rahmen des EU-Projekts »Smart Circular Bridge«. Die erste der drei Bioverbundwerkstoff-Brücken wurde 2022 im niederländischen Almere auf der Internationalen Gartenbauausstellung Floriade eingeweiht. Sie ist 15 Meter lang und trägt das Gewicht von rund 275 Personen gleichzeitig. Ein Konsortium verschiedener niederländischer und deutscher Hochschulen unter Leitung der Technischen Universität Eindhoven baute sie aus Flachs und einem speziellen Bioharz. Das Material ist trotz seines geringen Gewichts sehr stabil und hat vergleichbare Eigenschaften wie Aluminium oder Leichtstahlbau. Die Flachsbrücke ist mit fast 100 Sensoren ausgestattet, die in Echtzeit Daten über das Materialverhalten im alltäglichen Gebrauch liefern, die mit Hilfe künstlicher Intelligenz ausgewertet werden.
Digitale Brücken aus dem Drucker
Hanaa Dahy – als Gründerin und Leiterin der »BioMat«-Abteilung am Institut für Tragkonstruktionen der Universität Stuttgart – hat mit ihrem Team das Geländer der Flachsbrücke architektonisch entworfen. Wie sie berichtet, war es ein Kodesign-Prozess mit den Statikern der TU Eindhoven und der Firma, die das Geländer schließlich mit Robotern hergestellt hat. Bioverbundwerkstoffe (Biokomposite) sind ein zentrales Forschungsthema von Dahy. Ihr erstes Patent von inzwischen mehreren erhielt sie für den Einsatz von recycelten Strohfasern im Bau.
»Stroh als Reststoff der Agrarindustrie wird weltweit leider viel zu oft verbrannt«, berichtet sie. »Dabei ist Stroh eine wertvolle Ressource, bei deren Einsatz in der Konstruktion man sogar in beiden Sektoren den CO2-Fußabdruck reduziert: in der Landwirtschaft und im Bauwesen.« In Verbindung mit der maßgeschneiderten Faserplatzierung – einem digital gesteuerten Fertigungsprozess, den Architekten und Ingenieure aus der Textil- und Flugzeugbauindustrie übernommen und angepasst haben – konnten auch andere tragende Elemente wie Säulen oder Decken umgesetzt werden, erzählt Dahy. Oder Leichtbaupavillons, wie sie beispielsweise in Stuttgart und Freiburg zu besichtigen sind.
Die Teilnehmer des Brücken-Forschungsprojekts sind davon überzeugt, dass sie in Zukunft Brücken mit deutlich größeren Spannweiten und Lasten bauen werden. Dann könnte die Almere-Flachsbrücke als weltweit erstes Bauwerk dieser Art Schule machen, hoffen die Projektleiter: »Allein bei den Brücken lohnt es sich, über alternative Materialien nachzudenken, denn in den nächsten Jahren müssen in Europa zehntausende Brücken ersetzt werden.«
Wenn Sie inhaltliche Anmerkungen zu diesem Artikel haben, können Sie die Redaktion per E-Mail informieren. Wir lesen Ihre Zuschrift, bitten jedoch um Verständnis, dass wir nicht jede beantworten können.