Elektroautos: Was, wenn die Akkus ausgehen?
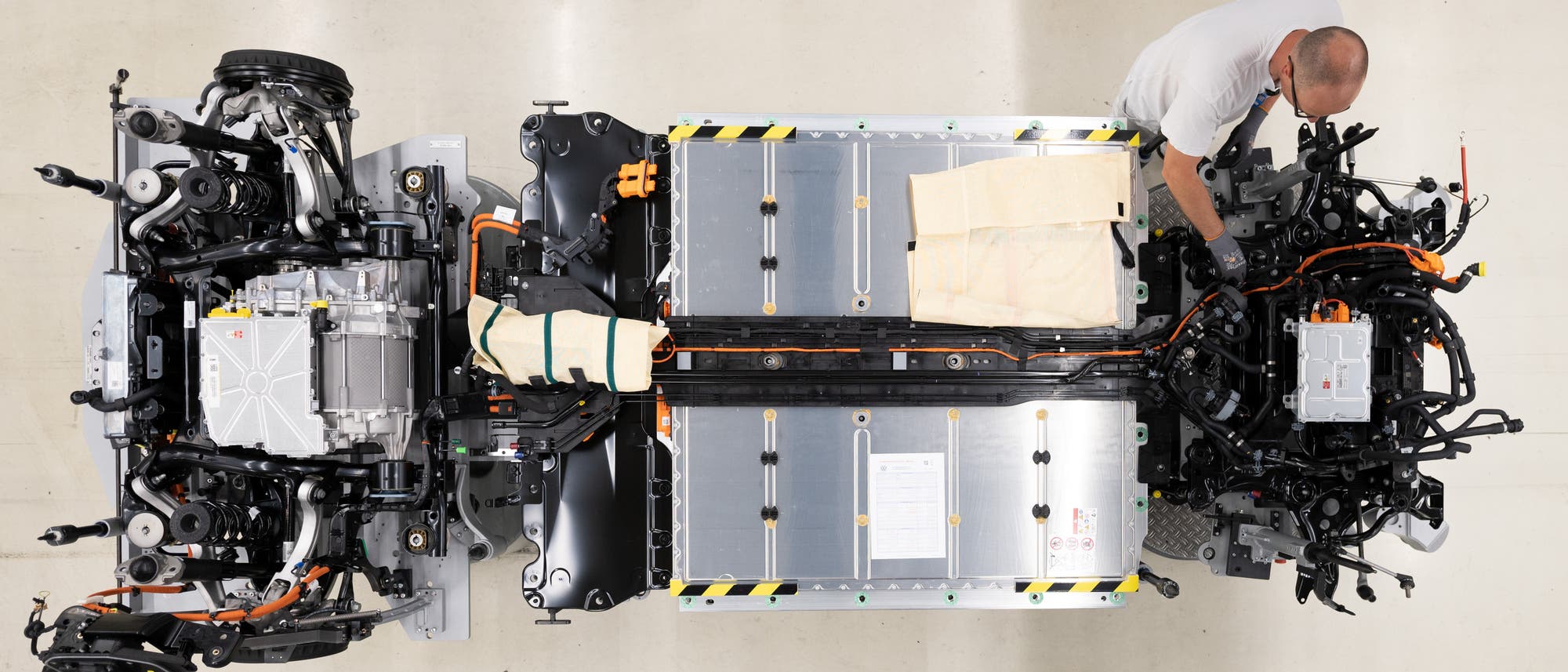
Das Zeitalter des Elektroautos ist endgültig angebrochen. Anfang 2021 kündigte der US-Autogigant General Motors an, er wolle den Verkauf von Benzin- und Dieselmodellen bis 2035 einstellen. Audi in Deutschland plant Ähnliches: Der Konzern gab bekannt, die Produktion von Benzinern und Dieselfahrzeugen bis 2033 zu beenden. Viele andere multinationale Automobilkonzerne haben vergleichbare Pläne vorgelegt. Lange haben die Hersteller auf die Bremse getreten, wenn es darum ging, ihre Autoflotten auch elektrisch fahren zu lassen – doch plötzlich scheinen sie Gas zu geben.
Die Elektrifizierung des Pkw-Bereichs nimmt in einer Weise Fahrt auf, von der selbst die eifrigsten Befürworter noch vor wenigen Jahren nicht zu träumen gewagt hätten. Und in vielen Ländern werden Verordnungen den Wandel noch beschleunigen. Aber auch ohne gesetzliche Maßnahmen wird laut der Londoner Consulting-Firma BloombergNEF (BNEF) im Jahr 2035 die Hälfte der weltweit verkauften Pkw elektrisch sein.
Diese massive Umstellung markiere einen »Übergang von einem kraftstoffintensiven zu einem materialintensiven Energiesystem«, erklärte die Internationale Energieagentur (IEA) im Mai 2021. In den kommenden Jahrzehnten werden hundert Millionen von Fahrzeugen mit zahllosen Batterien auf den Straßen unterwegs sein. Jeder dieser Akkus wird dutzende Kilogramm an Materialien enthalten, die allerdings erst noch abgebaut werden müssen. So besteht heute ein Lithium-Ionen-Akkupack vom Typ NMC532 gemäß dem Argonne National Laboratory in Lemont etwa aus 8 Kilogramm Lithium, 35 Kilogramm Nickel, 20 Kilogramm Mangan und 14 Kilogramm Kobalt.
Das Recycling wird eine Schlüsselrolle spielen
Damit es irgendwann eine Welt ausschließlich mit E-Autos geben kann, versuchen Materialwissenschaftler zwei Hauptprobleme zu lösen: Zum einen wollen sie in den Batterien die Zahl der Metalle verringern, die selten, teuer oder problematisch sind, weil ihr Abbau mit hohen Umwelt- und Sozialkosten verbunden ist. Zum anderen geht es darum, das Batterierecycling zu verbessern, damit die wertvollen Metallbestandteile effizient wiederverwendet werden. »Recycling wird in diesem Mix eine Schlüsselrolle spielen«, sagt Kwasi Ampofo, Bergbauingenieur und leitender Analyst bei BNEF.
»Das größte Problem ist das Geld«Jeffrey Spangenberger, Chemieingenieur, Argonne National Laboratory in Lemont
Batterie- und Automobilhersteller investieren derzeit in entsprechende Forschung – teils, weil es staatliche Anreize gibt, und teils, weil sie davon ausgehen, dass künftig stärker reguliert werden wird. Da es in den meisten Fällen immer noch billiger ist, Metalle abzubauen, als sie zu recyceln, wollen Forscher Verfahren entwickeln, mit denen wertvolle Metalle so preiswert zurückgewonnen werden, dass sie mit frisch abgebauten Rohstoffen konkurrieren können. »Das größte Problem ist das Geld«, sagt Jeffrey Spangenberger, Chemieingenieur am Argonne National Laboratory, der eine von den USA finanzierte Initiative zum Recycling von Lithium-Ionen-Batterien namens ReCell leitet.
Die Zukunft des Lithiums
Lithium-Ionen-Batterien werden in absehbarer Zeit wohl nicht durch andere Technologien ersetzt werden können. Ihre Kosten sind nämlich drastisch gesunken, obwohl die Energiespeicher deutlich mehr leisten als früher. Akkus sind heute 30-mal billiger als zu Beginn der 1990er Jahre. Damals sind sie als kleine, tragbare Batterien auf den Markt gekommen. BNEF geht davon aus, dass die Kosten für ein Lithium-Ionen-Akkupack für Elektroautos bis 2023 auf unter 100 US-Dollar pro Kilowattstunde sinken werden. Das wären etwa 20 Prozent weniger als heute. Infolgedessen dürften Elektroautos – die immer noch teurer sind als herkömmliche Fahrzeuge – bis Mitte der 2020er Jahre ungefähr genauso viel kosten wie Benziner und Dieselautos. Einigen Schätzungen zufolge sind Elektroautos über ihre gesamte Lebensdauer hinweg bereits jetzt billiger als Benziner, da sie weniger Kosten für Antrieb und Wartung verursachen.
Für die Entwicklung neuer Batterieformen ist die Konstruktionsweise der Akkus entscheidend. Heutzutage sind sie folgendermaßen aufgebaut: Um Strom zu erzeugen, transportieren die Batterien Lithium-Ionen von einer Schicht, der Anode, zur anderen, der Kathode. Beide Schichten sind durch eine weitere Lage getrennt, den Elektrolyten. Die Leistung der Akkus wird durch die Kathode begrenzt; darin sind die wertvollsten Metalle verbaut. Die Kathode einer typischen Lithium-Ionen-Batteriezelle besteht aus einer dünnen Schicht, die mikroskopisch kleine Kristalle enthält. Diese ähneln in ihrer Struktur oft Mineralen, die in der Erdkruste oder im Erdmantel vorkommen, wie solchen aus der Olivingruppe oder Spinellen. Die Kristalle verbinden negativ geladenen Sauerstoff mit positiv geladenem Lithium und verschiedenen anderen Metallen – in den meisten Elektroautos handelt es sich hierbei um eine Mischung aus Nickel, Mangan und Kobalt. Beim Aufladen einer Batterie werden Lithium-Ionen aus diesen Oxidkristallen herausgelöst und von einer Anode auf Graphitbasis angezogen, wo sie zwischen Schichten von Kohlenstoffatomen gespeichert werden.
© M. S. Ziegler & J. E. Trancik Energy Environ. Sci. (2021). / https://doi.org/grhx
Sinkende Kosten
Der Preis für Lithium-Ionen-Batterien ist seit 1991 um mehr als 97 Prozent gefallen.
Lithium selbst ist nicht knapp. Einem BNEF-Bericht vom Juni 2021 zufolge müssten die vorhandenen Reserven – 21 Millionen Tonnen laut dem US Geological Survey – ausreichen, um die Umstellung auf Elektrofahrzeuge bis Mitte des Jahrhunderts zu bewältigen. Diese Zahlen können sich allerdings noch ändern, denn sie beschreiben eine Menge, die zu den aktuellen Preisen und unter Berücksichtigung der heute verfügbaren Technologien sowie der geltenden behördlichen Anforderungen abgebaut wird. Doch für die meisten Materialien gilt: Wenn die Nachfrage wächst, steigen auch die förderbaren Mengen.
Die Lithiumnachfrage wird um das Siebenfache anwachsen
Um mehr E-Autos auf die Straße zu bringen und die entsprechend gestiegene Nachfrage zu befriedigen, muss die Lithiumproduktion gesteigert werden, sagt Ampofo. Die Nachfrage »wird zwischen 2020 und 2030 um das Siebenfache anwachsen«. Dies könnte zu vorübergehenden Engpässen und dramatischen Preisschwankungen führen, davon ist Ampofo überzeugt. Doch langfristig wird sich die Prognose kaum ändern, der Markt also Wege finden, sich anzupassen: »Wenn mehr Kapazitäten in der Produktion geschaffen werden, sollten sich diese Engpässe von selbst lösen«, sagt Haresh Kamath, Spezialist für Energiespeicher am Electric Power Research Institute im kalifornischen Palo Alto.
Eine Zunahme des Lithiumabbaus bringt allerdings einige Umweltprobleme mit sich: Die derzeitigen Formen der Gewinnung erfordern große Mengen an Energie (bei der Gewinnung von Lithium aus Gestein) oder Wasser (bei der Gewinnung aus Solen). Modernere Techniken zur Gewinnung von Lithium aus geothermischem Wasser gelten als umweltfreundlicher.
Noch größere Sorgen bereitet Forschern aber das Kobalt. Es stellt den teuersten und problematischsten Bestandteil der Akkus für Elektrofahrzeuge dar. Zwei Drittel des weltweiten Bedarfs deckt der Abbau in der Demokratischen Republik Kongo. Menschenrechtsaktivisten haben längst angemahnt, dass die dortigen Arbeitsbedingungen völlig unzureichend sind. Besonders problematisch sind Kinderarbeit und die Gesundheitsschädigung der Arbeiter. Wie andere Schwermetalle ist auch Kobalt bei unsachgemäßem Umgang giftig. Dabei existieren alternative Ressourcen, die erschlossen werden könnten – beispielsweise metallreiche »Knollen«, die auf dem Meeresboden gefunden werden. Allerdings bergen auch sie Gefahren für die Umwelt, sollten sie abgebaut werden. Und letztlich könnte es zu Engpässen in der Förderung von Nickel kommen, einem weiteren wichtigen Bestandteil von Batterien.
Gibt es eine Lösung für Kobalt?
Um die Probleme mit den Rohstoffen zu lösen, experimentieren einige Labore mit kobaltarmen oder -freien Kathoden. Doch die Materialien für Kathoden müssen sorgfältig entwickelt werden, damit ihre Kristallstrukturen nicht zerbrechen, selbst wenn sich mehr als die Hälfte der Lithium-Ionen während des Ladevorgangs von ihnen löst. Ganz auf Kobalt zu verzichten, würde die Energiedichte der Batterie senken, sagt der Materialwissenschaftler Arumugam Manthiram von der University of Texas in Austin, weil sich dadurch die Kristallstruktur der Kathode und ihre Fähigkeit, Lithium zu binden, verändern.
Zumindest im Labor hat sich das Problem bereits lösen lassen. Manthiram und seine Kollegen haben gezeigt, dass Kobalt aus den Kathoden entfernt werden kann, ohne die Batterieleistung zu beeinträchtigen. »Das kobaltfreie Material, über das wir berichtet haben, hat die gleiche Kristallstruktur wie Lithium-Kobaltoxid und daher die gleiche Energiedichte«, sagt Manthiram. Das Team hat bei der Kathodenherstellung geringe Mengen anderer Metalle dazugegeben – unter Beibehaltung der Kobaltoxid-Kristallstruktur der Kathode. Laut Manthiram kann dieses Verfahren problemlos in bestehenden Fabriken eingesetzt werden. Er hat ein Start-up mit dem Namen TexPower gegründet, mit dem Ziel, sein Produkt innerhalb der nächsten zwei Jahre auf den Markt zu bringen. Auch andere Labors arbeiten an kobaltfreien Batterien: Insbesondere Tesla, der Pionier unter den Elektroautoherstellern, hat angekündigt, dass er Kobalt in den nächsten Jahren aus allen seinen Batterien entfernen will. Der Autobauer hat sogar erste E-Fahrzeuge mit kobaltfreien Akkus ausgestattet, die sich aber Berichten zufolge womöglich noch bewähren müssen.
Sun Yang-Kook von der Hanyang-Universität in Seoul meint hingegen, es könnte bei der Herstellung der neuen Kathoden technische Probleme geben. Der Materialwissenschaftler hat ähnliche Leistungen bei kobaltfreien Kathoden erzielt. Die Schwierigkeit sei dabei jedoch, dass das Verfahren auf der Veredelung von nickelhaltigen Erzen beruhe, wofür eine sehr teure reine Sauerstoffumgebung nötig sei. Allerdings sei in den Augen der meisten Forscher das Kobaltproblem bereits im Wesentlichen gelöst. Manthiram und Sun »haben gezeigt, dass man wirklich gute Materialien ohne Kobalt herstellen kann, die gut funktionieren«, sagt Jeff Dahn, Chemiker an der Dalhousie University in Halifax.
Manthiram und Sun »haben gezeigt, dass man wirklich gute Materialien ohne Kobalt herstellen kann, die gut funktionieren«Jeff Dahn, Chemiker, Dalhousie University in Halifax
Nickel ist zwar nicht so teuer wie Kobalt, aber auch nicht gerade billig. Forscherinnen und Forscher wollen daher Akkus ohne den Stoff produzieren. »Wir haben uns mit der Kobaltknappheit befasst, doch weil [der Markt] so stark wächst, steuern wir direkt auf ein Nickelproblem zu«, sagt der Materialwissenschaftler Gerbrand Ceder vom Lawrence Berkeley National Laboratory. Wenn Akkus sowohl ohne Kobalt als auch ohne Nickel auskommen sollen, müssen völlig neue Kristallstrukturen für die Kathoden entwickelt werden.
Ein Ansatz ist die Verwendung von Materialien, die als ungeordnete Steinsalze bezeichnet werden. Sie haben ihren Namen auf Grund ihrer kubischen Kristallstruktur, die der von Natriumchlorid ähnelt. Dabei übernimmt Sauerstoff die Rolle des Chlors, und eine Mischung aus Schwermetallen ersetzt das Natrium. In den letzten zehn Jahren haben Ceders Team und andere Arbeitsgruppen gezeigt: Bestimmte lithiumreiche Steinsalze sind so beschaffen, dass das Lithium in sie leicht eindringen und wieder daraus entweichen kann – eine entscheidende Eigenschaft, um wiederholtes Aufladen zu ermöglichen. Im Gegensatz zu herkömmlichen Kathodenmaterialien benötigen ungeordnete Steinsalze jedoch kein Kobalt oder Nickel, um während dieses Prozesses stabil zu bleiben. Sie können mit Mangan hergestellt werden, das billig und reichlich vorhanden ist, sagt Ceder.
Lässt sich das Recycling wirklich wirtschaftlich gestalten?
Wenn Batterien ohne Kobalt im großen Stil produziert werden sollten, könnte allerdings ein unbeabsichtigter Nebeneffekt entstehen: Damit sich das Recycling von Batterien rechnet, müssen die Metalle aufbereitet werden. Für die anderen Bestandteile, vor allem für Lithium, lohnt sich das Recycling nicht, weil sie derzeit preiswerter in der Förderung sind.
In einer typischen Recyclinganlage werden die Batterien zunächst zerkleinert, bis man eine pulvrige Mischung aller Materialien erhält. Dieses Gemisch wird dann in seine elementaren Bestandteile zerlegt, entweder durch Verflüssigung in einer Schmelze (Pyrometallurgie) oder durch Auflösen in Säure (Hydrometallurgie). Schließlich werden die Metalle in Form von Salzen aus der Lösung ausgefällt.
Die Forschung hat sich auf die Verbesserung des Verfahrens konzentriert, um recyceltes Lithium wirtschaftlich attraktiv zu machen. Die überwiegende Mehrheit der Lithium-Ionen-Batterien wird in China, Japan und Südkorea hergestellt; dementsprechend wachsen die Recyclingkapazitäten dort am schnellsten. Das in Foshan ansässige Unternehmen Guangdong Brunp – eine Tochtergesellschaft von CATL, Chinas größtem Hersteller von Lithium-Ionen-Batterien – kann nach Angaben eines Sprechers 120 000 Tonnen Akkus pro Jahr recyceln. Das entspricht der Menge, die in etwas mehr als 200 000 Autos verbaut wird. Das Unternehmen ist also offenbar in der Lage, den Großteil des Lithiums, Kobalts und Nickels zurückzugewinnen. Die Regierung unterstützt diese Entwicklung: In China gibt es bereits finanzielle und regulatorische Anreize für Batterieunternehmen, die Materialien von Recyclingfirmen zu beziehen, anstatt neu geförderte zu importieren, sagt Hans Eric Melin, Geschäftsführer von Circular Energy Storage, einem Beratungsunternehmen in London.
Die Probleme, die beim Recyceln entstehen
Die Europäische Kommission plant strenge Anforderungen für das Batterierecycling, die ab 2023 eingeführt werden könnten – obwohl die Aussichten für die Entwicklung einer eigenen Recyclingindustrie innerhalb der EU eher ungewiss sind. Die Regierung von US-Präsident Joe Biden will unterdessen Milliarden von Dollars investieren, um eine heimische Industrie zur Herstellung von Elektroautobatterien zu fördern und deren Recycling zu unterstützen. Bislang hat Bidens Regierung jedoch keine neuen Vorschriften verabschiedet, die über die bestehenden Regelungen hinausgehen, dass Batterien als Sondermüll behandelt und entsprechend sicher entsorgt werden müssen. Zusätzlich geben einige nordamerikanische Start-ups an, bereits die meisten Metalle einer Batterie – einschließlich Lithium – aufbereiten zu können; dafür fielen Preise an, die mit den Förderkosten mithalten könnten. Analysten betonen aber, dass derzeit nur das Kobalt diese Rechnung wirtschaftlich macht.
»Über 98 Prozent der Blei-Säure-Batterien werden recycelt«Haresh Kamath, Spezialist für Energiespeicher, Electric Power Research Institute in Palo Alto
Ein anderer Ansatz besteht darin, die Kathodenkristalle wiederzuverwenden, statt per Pyro- oder Hydrometallurgie ihre Struktur zu zerstören. ReCell, das von Spangenberger geleitete 13-Millionen-Euro-Projekt, umfasst drei Labore, drei Universitäten und zahlreiche Industrieunternehmen. Die Projektteilhaber arbeiten an Techniken, bei denen Recyclingfirmen die Kathodenkristalle extrahieren und weiterverkaufen können. Ein entscheidender Schritt besteht darin, nach dem Schreddern der Batterien die Kathodenmaterialien mit Hilfe von Hitze, Chemikalien oder anderen Methoden vom Rest zu trennen. »Wir wollen unbedingt die Kristallstruktur erhalten, weil es viel Energie und Knowhow gekostet hat, sie überhaupt zu erschaffen. Darin liegt ein großer Teil des Werts«, sagt Linda Gaines, physikalische Chemikerin am Argonne National Laboratory und Hauptanalystin von ReCell.
Die Wiederaufbereitungstechniken funktionieren mit einer Reihe von Kristallstrukturen und -zusammensetzungen, sagt Gaines. Wenn eine Recyclingfirma jedoch unterschiedliche Batterietypen erhält, landen verschiedene Arten von Kathodenmaterialien in der Aufbereitung. Das erschwert die Trennung der diversen Kristalltypen der Kathoden. Die von ReCell entwickelten Verfahren können zwar problemlos Nickel, Mangan und Kobalt von anderen Zelltypen abtrennen, aber es wird schwierig, Typen zu trennen, die Kobalt und Nickel in unterschiedlichen Anteilen enthalten. Deshalb sollten laut Spangenberger die Batterien mit einer Art standardisiertem Strichcode versehen sein, der den Recyclern verrät, was in den Akkus steckt.
Die Batterien müssen sich leichter auseinandernehmen lassen
Ein weiteres potenzielles Hindernis besteht darin, dass sich die chemische Zusammensetzung der Kathoden ständig weiterentwickelt. Die Kathoden, die die Hersteller in 10 bis 15 Jahren verwenden werden – also dann, wenn heute hergestellte E-Autos abgewrackt werden –, könnten sich sehr wohl von den jetzigen unterscheiden. Am effizientesten wäre es daher, wenn die Hersteller ihre Batterien selbst zurücknehmen. Außerdem sollten die Batterien von Grund auf so konzipiert werden, dass sie sich leichter auseinandernehmen lassen, fügt Gaines hinzu.
Das Recycling wäre viel rentabler, wenn die Batteriezellen nicht geschreddert, sondern zerlegt würden – davon ist der Materialwissenschaftler Andrew Abbott von der University of Leicester überzeugt. Er und sein Team haben eine Technik entwickelt, bei der das Kathodenmaterial mit Hilfe von Ultraschall herausgetrennt wird. Die Methode funktioniert am besten bei Batteriezellen, die flach verpackt und nicht aufgerollt sind (wie die üblichen »zylindrischen« Batterien). Abbott fügt hinzu, dass recycelte Materialien auf diesem Weg viel billiger würden als neu abgebaute Metalle. Er ist an einem mit zirka 16 Millionen Euro dotierten Forschungsprogramm der britischen Regierung zur Nachhaltigkeit von Batterien beteiligt, das den Namen ReLiB trägt.
Unabhängig davon, welche Recyclingverfahren sich durchsetzen werden, das Maß macht die Sache rentabel. Obwohl in Medienberichten die befürchteten Massen von Altbatterien oft als drohende Krise beschrieben werden, sehen Analysten darin eine große Chance, sagt Hans Eric Melin. Sobald Millionen von Großbatterien das Ende ihrer Lebensdauer erreicht haben, werden entsprechend größere Recyclingkapazitäten die Aufbereitung effizienter machen – und den wirtschaftlichen Nutzen erhöhen.
Die klassische Autobatterie gibt Anlass zur Hoffnung
Aus der Perspektive von Experten gibt ausgerechnet die klassische Autobatterie – die Blei-Säure-Batterie – Anlass, optimistisch zu sein. Da Blei giftig ist, werden diese Batterien als Sondermüll eingestuft und müssen sicher entsorgt werden. Doch obwohl Blei auch billig ist, hat sich eine effiziente Recyclingindustrie entwickelt. »Über 98 Prozent der Blei-Säure-Batterien werden recycelt«, sagt Haresh Kamath. »Der Wert einer solchen Batterie ist sogar geringer als der eines Lithium-Ionen-Akkus. Aber wegen der Mengen ist es trotzdem sinnvoll, sie zu recyceln«, sagt Melin.
Es könnte noch eine Weile dauern, bis der Markt für Lithium-Ionen-Batterien seine mögliches Potenzial erreicht hat, auch weil diese Batterien außergewöhnlich langlebig geworden sind: Die heutigen Autobatterien können bis zu 20 Jahre lang halten, sagt Kamath. In einem typischen Elektroauto, das zurzeit verkauft wird, überdauert das Batteriepack länger als das dazugehörige Fahrzeug, erklärt Melin.
Das heißt, wenn alte Elektroautos verschrottet werden, werden die Batterien oft weder weggeworfen noch recycelt. Stattdessen werden sie ausgebaut und für weniger leistungsfordernde Geräte wiederverwendet wie stationäre Energiespeicher oder Antriebe für Boote. Nach zehn Jahren Nutzung hat eine Autobatterie wie die eines Nissan Leaf, die ursprünglich 50 Kilowattstunden fasste, höchstens 20 Prozent ihrer Kapazität verloren.
Im Mai 2021 prognostizierte die IEA, die für ihre zurückhaltenden Vorhersagen bekannt ist, in einem weiteren Bericht, dass die Umstellung auf elektrische Fahrzeuge einen Hauptfaktor darstellt, wenn die Welt bis Mitte des Jahrhunderts ihr Netto-Null-Ziel erreichen will. Politiker, Forscher und Hersteller sind sich einiger denn je, dass dieses Ziel machbar ist und dass die Probleme bei der Elektrifizierung von Autos inzwischen gelöst werden können. Zudem wissen alle Beteiligten, dass es keine Zeit mehr zu verlieren gibt, wenn wir den Klimawandel noch bremsen wollen.
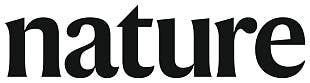
Wenn Sie inhaltliche Anmerkungen zu diesem Artikel haben, können Sie die Redaktion per E-Mail informieren. Wir lesen Ihre Zuschrift, bitten jedoch um Verständnis, dass wir nicht jede beantworten können.