Rohstoffe: Wächst die Zukunft der Chemieindustrie auf dem Acker?
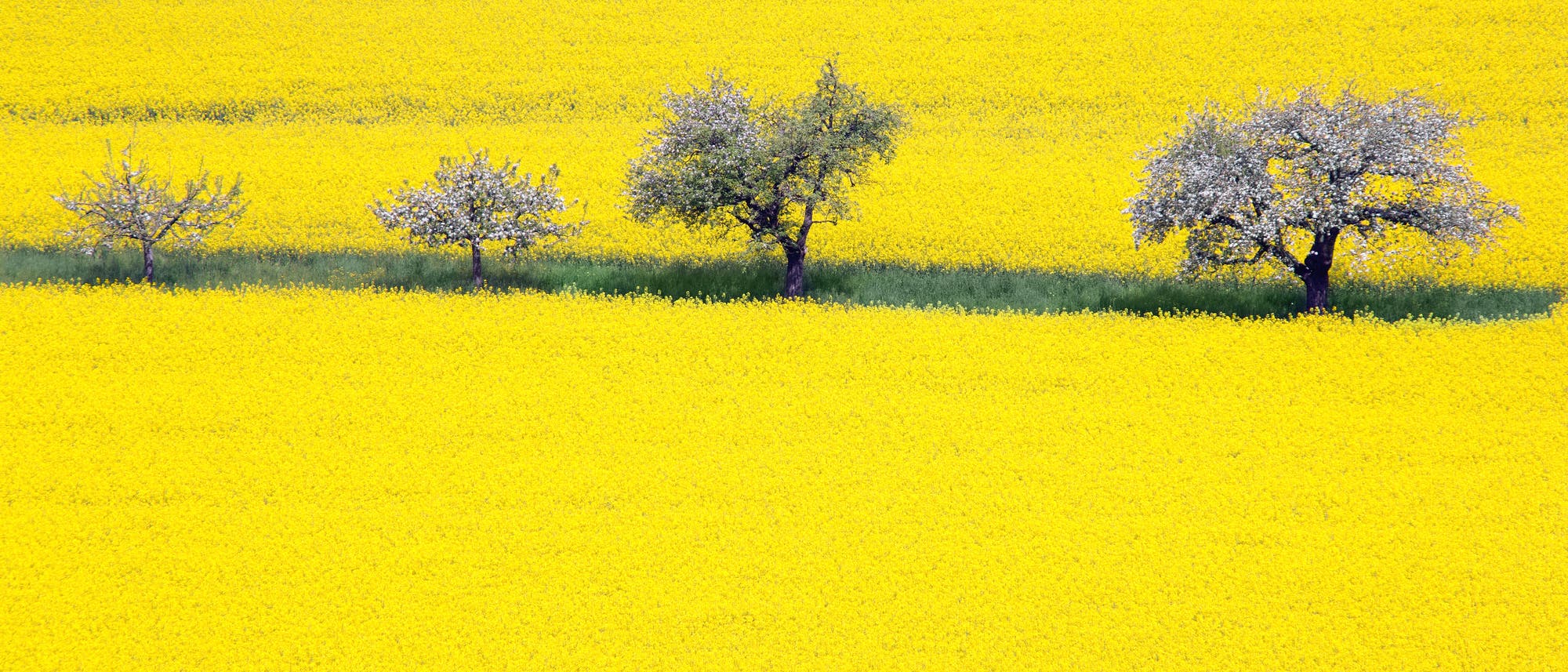
Erdöl, Kohle und Erdgas sind endlich, und das stellt die chemische Industrie vor ein Problem. Das Rohmaterial für Kunststoffe einfach vom Acker oder aus dem Wald zu holen, das klingt verlockend. Und es ist möglich. Neu ist diese Idee genau genommen nicht: Schließlich köchelten bereits die Neandertaler vor 200 000 Jahren die Rinde von Birken so lange im Feuer, bis daraus erst Teer und später Pech entstand. Chemiker nennen diesen Vorgang eine Pyrolyse, aus den Biomolekülen der Birkenrinde stellten die Neandertaler einen Urzeitkunststoff her. Dieses so entstandene Birkenpech war eine Art Alleskleber der Steinzeit, mit dem man zum Beispiel Steinspitzen fest an einen Holzschaft heften konnte.
Exakt mit dieser Methode hatte der Steinzeitmann Ötzi vor mehr als 5000 Jahren in den Alpen an seine Pfeilschäfte aus dem Holz des Wolligen Schneeballs kunstvoll aus Feuerstein geschlagene Spitzen geklebt. Obendrein konnte man mit diesem Pech zum Beispiel Boote wasserdicht machen, was in der biblischen Bauanleitung für die Arche Noah schriftlich festgehalten ist, tatsächlich aber schon viel früher steinzeitliche Bootsbauer angewendet hatten.
Auch der erste Kunststoff des Industriezeitaltes wurde aus nachwachsenden Rohstoffen hergestellt: Kampfer wurde aus dem Holz, den Zweigen und Blättern des Kampferbaums destilliert, während das auch als Schießbaumwolle bekannte Zellulosenitrat mit einem Gemisch aus Salpeter- und Schwefelsäure aus Baumwolle produziert wurde. Mischte man beide Substanzen, erhielt man Zelluloid, dessen erste Anwendung die preiswerte Herstellung von Billardkugeln war, die vorher aus Elfenbein waren.
Bald danach ersetzte man andere teure Naturprodukte wie Bernstein, Ebenholz oder Schildpatt durch erheblich billigere Massenprodukte aus Zelluloid, das obendrein noch zu einem durchsichtigen Träger für Fotos und Filme weiterentwickelt wurde. Erst als Erdöl in großen Mengen gefördert und verarbeitet wurde, verdrängten vielerorts billigere, fossile Alternativen die nachhaltigen Kunststoffe und Rohmaterialien. Seit der Jahrtausendwende schlägt das Pendel jedoch zurück und »grüne« Produkte werden in der chemischen Industrie, aber auch von anderen Sparten wie der Automobilindustrie wieder häufiger eingesetzt.
Trabant als Vorreiter
Allerdings waren die Naturprodukte zwischenzeitlich nicht vollständig verschwunden, sondern hatten in einigen Nischen überlebt. Eine davon war die DDR. Dort stellte man die Karosserie des Trabants aus Phenolharzen her, die mit Baumwollfasern verstärkt wurden. Der Spitzname »Plastikbomber« war also durchaus treffend gewählt. Und er hatte nicht von der Hand zu weisende Vorteile. So sind solche mit Fasern aus der Natur verstärkten Kunststoffe ähnlich wie Stahlblech mechanisch stark belastbar, aber deutlich leichter. Ihr Einsatz senkt daher den Energieverbrauch eines Fahrzeugs.
Auch aus diesem Grund werden heute vor allem im Fahrzeuginnenraum verschiedene Bauteile wie Armaturenbrett und Hutablage sowie Kofferraum- und Türverkleidungen aus Kunststoff angefertigt, der mit Hanf, Flachs oder Jute verstärkt ist. Solche Verbundwerkstoffe sind deutlich leichter als herkömmliche, glasfaserverstärkte Kunststoffe. Obendrein benötigt ihre Herstellung zwischen 25 und 75 Prozent weniger Energie. Rechnet man den in den Naturfasern steckenden Kohlenstoff mit ein, erspart das dem Klima zwischen 28 und 74 Prozent des Treibhausgases Kohlendioxid.
Bisher wird der Kunststoff dieser Werkstoffe allerdings meist aus Erdöl produziert, weil das heutzutage noch billiger ist. »Die Naturfasern können jedoch auch in Harze eingebettet werden, die aus Naturstoffen hergestellt werden«, erklärt Dietmar Peters von der Fachagentur Nachwachsende Rohstoffe (FNR) in Gülzow-Prüzen in Mecklenburg-Vorpommern. Ausbaufähig ist sicher auch die Verwendung außerhalb des Automobilbaus: 2015 wurden in Europa von 92 000 Tonnen mit Naturfasern verstärkten Kunststoffen gerade einmal 2000 Tonnen nicht für Autos, sondern für andere Zwecke zum Beispiel für das Herstellen von Geigenkoffern eingesetzt.
Deutlich anders sieht die Situation bei Kunststoffen aus, die mit Holzmehl oder -spänen aus Sägewerken gefüllt oder verstärkt werden. Zwar landeten von den 2015 in Europa so hergestellten 260 000 Tonnen Kunststoffen satte 60 000 Tonnen im Automobilbau. Mit 174 000 Tonnen wurden aber erheblich größere Mengen zu Terrassendielen verarbeitet, die vor allem tropische Hölzer ersetzen. Da solche Werkstoffe zum Beispiel zu 30 Prozent aus Polypropylen bestehen, dessen Grundstoff Erdöl ist, und zu 70 Prozent aus Holzmehl, das meist von heimischen Nadelhölzern stammt, schonen solche Werkstoffe also tropische Wälder.
Nachhaltig auf dem Nürburgring
Auch beim Automobilbau soll die Entwicklung nicht bei Hutablagen und Kofferraumverkleidungen aus nachwachsenden Rohstoffen stehen bleiben. So fördert die FNR seit 2011 Studien zu einem BioHybridCar, die von der Hochschule Hannover, dem Fraunhofer-Institut für Holzforschung in Hannover und dem Motorsport-Marketingunternehmen Four Motors in Reutlingen vorangetrieben werden. Dabei werden wichtige Karosserieteile wie zum Beispiel die Fahrzeugtüren aus Flachsfasergewebematten in die benötigte Form gelegt, mit einem Harz aus Erdöl oder später aus Sonnenblumen- oder Leinöl getränkt und vollständig ausgehärtet.
Diese Teile sind erheblich leichter als der bisher verwendete Stahl: Während eine herkömmliche Seitentür 38,5 Kilogramm wiegt, bringt die mit Pflanzenfasern verstärkte Kunststofftür gerade einmal 14 Kilogramm auf die Waage. Im Durchschnitt liegt die Gewichtsersparnis bei verschiedenen Fahrzeugteilen bei 60 Prozent, was sich bei einem VW-Scirocco-Rennwagen auf insgesamt 67 Kilogramm addiert.
Das senkt den Energieverbrauch enorm. Obendrein sind solche Werkstoffe viel preiswerter als Kohlefasern. Beim 24-Stunden-Rennen auf dem Nürburgring absolvieren diese Fahrzeuge einen harten Praxistest, den 2018 die drei eingesetzten Teilplastik-Porsche-Rennfahrzeuge mit Bravour bestanden. Dabei sollen solche Wettbewerbe den Weg für Verbundwerkstoffe zum Energiesparen in normalen Straßenfahrzeugen ebnen.
Autoreifen aus Löwenzahn
Diese Alltagsautos fahren dann vermutlich auf Reifen, deren Gummi aus Löwenzahnpflanzensaft stammt. Nachhaltig kann man solche Reifen zwar aus Naturkautschuk herstellen. Allerdings wachsen die dafür benötigten Kautschukbäume nur in den Tropen, und die Plantagen dort können die Nachfrage nach diesem Rohstoff für Reifen, Latexhandschuhe in Krankenhäusern, Kondome und eine ganze Reihe weiterer Produkte bei Weitem nicht decken. Daher stammt heute 60 Prozent des weltweit verwendeten Kautschuks nicht aus tropischen Plantagen, sondern aus Erdöl. Das wiederum spürt der Autofahrer an der Qualität: Die technischen Eigenschaften dieses synthetischen Kautschuks sind deutlich schlechter als beim Naturprodukt. Kein Wunder, wenn der Naturkautschukmarkt im Jahr 2011 bereits 20 Milliarden US-Dollar umgesetzt hat.
Als Alternative diente bereits im Zweiten Weltkrieg der Russische Löwenzahn Taraxacum koksaghyz. Der weiße Pflanzensaft dieses Gewächses hat ähnliche Eigenschaften wie Naturkautschuk. Die FNR hat daher gute Gründe, bis November 2019 im Projekt TAKOWIND II diesen Pflanzensaft vom Hersteller Continental Reifen Deutschland und weiteren Unternehmen, den Universitäten Münster und Regensburg sowie dem Julius Kühn-Institut – Bundesforschungsinstitut für Kulturpflanzen genauer untersuchen zu lassen.
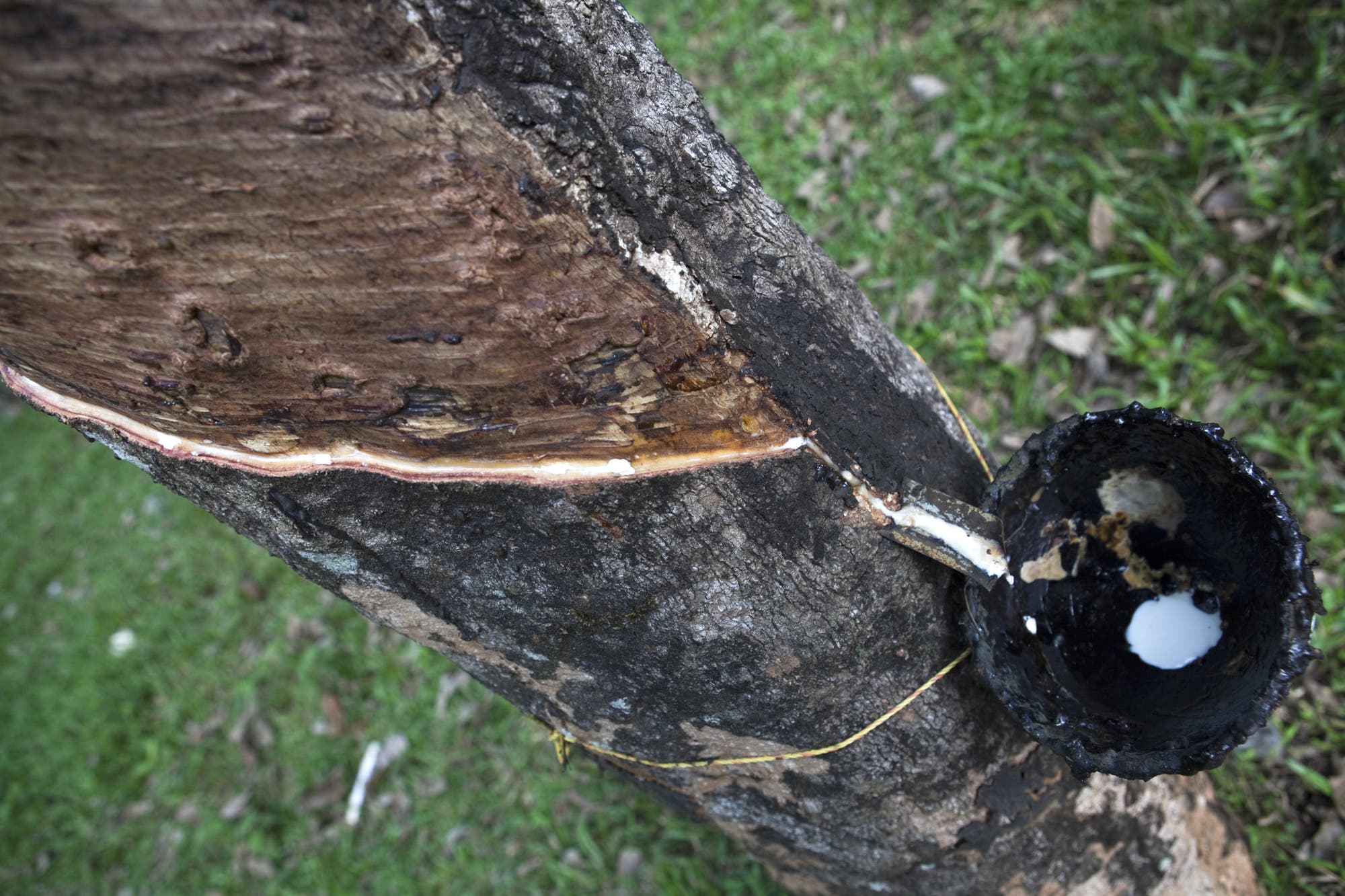
Dabei soll nicht nur die Züchtung des Löwenzahns intensiviert und beschleunigt, sondern auch der Latexertrag der Pflanzen auf zehn Prozent verbessert und die Grundlagen für einen kommerziellen Anbau gelegt werden. Unter anderem wird in einem Teilprojekt eine Erntemaschine für Löwenzahn entwickelt. Dahinter steckt natürlich auch der Gedanke, Deutschland und die Europäische Union von Importen dieses Rohstoffs unabhängig zu machen. Immerhin fällt Kautschuk eine strategische Schlüsselrolle zu, weil ohne ihn kein Autoreifen rollen würde.
Gut geschmiert dank einer Million Tonnen Schmieröl pro Jahr
Weniger im Blickpunkt von Autofahrern stehen normalerweise Schmieröle, meist tauchen sie nur als Posten »Motoröl« auf der Kundendienstrechnung auf. Diese Substanzen verringern die Reibung erheblich und lassen bewegliche Teile zum Beispiel in einem Motor aneinander vorbeigleiten – ohne Schmieröle würde sich in der modernen Technik wenig bewegen. Da wundert es nicht, wenn in Deutschland jedes Jahr rund eine Million Tonnen Schmieröle in Motoren und Getrieben, Hydraulik und vielen anderen Bereichen wie Planeten- und Schneckengetrieben für die Verpackungsindustrie eingesetzt werden. Allerdings liegt der Bioanteil nach FNR-Angaben im Jahr 2018 nur bei rund 35 000 Tonnen, immerhin mit steigender Tendenz.
Technische Gründe dürften diesem Unterschied eigentlich nicht zu Grunde liegen. Die häufig aus Raps hergestellten Bioschmieröle erreichen die technischen Eigenschaften der aus Erdöl produzierten Konkurrenz ohne Probleme, oft übertreffen sie diese deutlich. Das hat allerdings seinen Preis, so kostet ein Hydrauliköl vom Acker mehr als das Dreifache des herkömmlichen Produkts.
Andererseits altert das Bioprodukt auch langsamer und hält daher länger, statt nach 2000 Betriebsstunden ist ein Ölwechsel zum Beispiel erst nach 6000 Stunden fällig. Rechnet man alle Faktoren wie die Arbeitszeit für einen Ölwechsel mit ein, summieren sich die herkömmlichen Ölkosten für eine 60-Tonnen-Bagger laut FNR auf 1,27 Euro pro Betriebsstunde, während das Bioöl mit rund zehn Prozent höheren Kosten und 1,39 Euro pro Stunde zu Buche schlägt.
Bioöl ist biologisch abbaubar – was ein großer Vorteil ist
Nicht einberechnet sind dabei einige schwer zu beziffernde Vorteile für das Bioprodukt: Durch die höhere Ölqualität ist der Verschleiß deutlich geringer, weil der Ölwechsel seltener anfällt, muss die Arbeit weniger oft unterbrochen werden. Und bei einem Unfall sind die Kosten niedriger, weil das Bioöl in der Umwelt rasch abgebaut wird.
Aus diesem Grund hat sich die biologische Alternative bei Kettensägen längst durchgesetzt und erreicht dort einen Marktanteil von mehr als 80 Prozent: Ein kleiner Teil dieses Kettenöls wird nämlich verbraucht und gelangt in die Umwelt. Und dort ist die biologische Abbaubarkeit natürlich sehr gefragt. Einen ähnlichen Siegeszug könnten auch andere Geräte antreten – vor allem, wenn der Preis sinken sollte. So scheint es möglich, den Ölwechsel beim Hydraulikbagger statt nach 6000 erst nach 10 000 Betriebsstunden zu machen, was die Ölkosten auf 1,09 Euro pro Betriebsstunde und damit deutlich unter die Werte von herkömmlichen Schmiermitteln senken dürfte.
Knapp 1,2 Million Tonnen Pflanzenöle und -fette werden in Deutschland jedes Jahr in chemischen und technischen Verfahren eingesetzt. Gerade einmal vier Prozent davon werden zu Schmierölen verarbeitet. Ganz anders sieht die Situation nach Angaben der FNR dagegen bei Wasch-, Pflege- und Reinigungsmitteln aus, die mehr als die Hälfte des Marktes bei Pflanzenölen und -fetten beanspruchen und dabei Kokos- und Palmöl bevorzugen. Viele Tenside aber werden mittlerweile auch aus Zucker gewonnen, der entweder aus heimischen Zuckerrüben oder tropischem Zuckerrohr stammt.
Trotzdem sind nachwachsende Wasch-, Pflege- und Reinigungsmittel immer noch ein Nischenprodukt: Gerade einmal sieben Prozent der für die Reinigungswirkung entscheidenden Tenside in Wasch- und Reinigungsmitteln stammen in Deutschland aus nachwachsenden Rohstoffen. Die Hälfte kommt dagegen immer noch aus Erdöl und Co, während der Rest aus beiden Quellen gemischt ist. Auch im Waschmittelmarkt haben pflanzenbasierte Rohstoffe also durchaus noch Luft nach oben.
»700 000 Tonnen Pflanzenstärke wandern jedes Jahr in Deutschland in die Papierindustrie«Dietmar Peters
Bei den 2017 in Deutschland produzierten 22,9 Millionen Tonnen Papier, Pappe und Karton ist der Spielraum zu mehr Nachhaltigkeit dagegen bereits recht gut ausgeschöpft: Papier wird nach wie vor aus der im Holz vorhandenen Zellulose und damit aus einem nachwachsenden Rohstoff hergestellt und natürlich aus Altpapier recycelt. Das wird vermutlich noch eine Weile so bleiben, weil die Digitalisierung bedrucktes Papier zwar durchaus zurückdrängen könnte, andererseits aber der Internethandel boomt – und damit der Kartonbedarf.
Vor seiner Verwendung wird Papier fast immer beschichtet. Dadurch wird es reißfester und übersteht so zum Beispiel die starken Kräfte in den immer schneller laufenden Druckmaschinen besser. Diese Beschichtung kann als Acrylat ein Erdölprodukt sein – oder sie kommt in Form von Weizenstärke direkt vom Acker. »700 000 Tonnen Stärke wandern jedes Jahr in Deutschland in die Papierindustrie«, erklärt FNR-Experte Dietmar Peters. »Außerhalb des Lebensmittelbereichs ist das inzwischen die wichtigste Anwendung von Pflanzenstärke.« Da wundert sich niemand mehr, wenn die Stärkeindustrie in Deutschland längst ein eigenes Labor für solche Papierbeschichtungen unterhält.
Naturstoff-Boom
Dieser Naturstoff-Boom hat seine Gründe: Stärke baut sich genau wie Kunststoffe aus kleineren Einheiten auf, die zu einer langen Kette miteinander verknüpft sind. Um dem Nachwuchs in Form eines Samens einen guten Start ins Leben zu geben, schicken ihn verschiedene Pflanzen wie Weizen oder Kartoffeln mit einem Energievorrat in die Welt. Dazu verknüpfen sie einzelne Moleküle des Zuckers Glukose zu so genannten Polysaccharidketten und erhalten so einen besonders haltbaren Energiespeicher, der auch nach einigen Jahren noch reichlich Power hat. Die Zucker lassen sich aber auch ein wenig anders als in Stärke miteinander verknüpfen. Aus der gleichen Glukose entsteht der sehr feste Baustoff Zellulose, der die Wände von Pflanzenzellen stabilisiert und der zur häufigsten organischen Verbindung auf der Erde wurde.
Polymere nennen Chemiker solche langen Ketten, die bereits die Neandertaler oder der Steinzeitmann Ötzi in den Alpen als Birkenpech nutzten. In der zweiten Hälfte des 19. Jahrhunderts beginnt mit dem aus Baumwolle und Kampfer hergestelltem Zelluloid dann der Siegeszug der Kunststoffe, die zunächst einmal aus nachwachsenden Rohstoffen synthetisiert wurden.
Das änderte sich erst, als Erdöl billig zur Verfügung stand. Daraus werden kleine, organische Moleküle gewonnen, die sich ähnlich wie Glukose zu längeren Ketten verknüpfen lassen. Solche Polymere können aus verschiedenen kleinen Molekülen hergestellt und mit einfachen chemischen Reaktionen auch noch verändert werden. Obendrein können Beimischungen anderer Substanzen einen Kunststoff erheblich verändern und ihn zum Beispiel elastischer oder steifer machen. Auf dieser Grundlage produziert die chemische Industrie heute eine ganze Palette von Kunststoffen mit zum Teil sehr unterschiedlichen Eigenschaften.
Renaissance nachwachsender Rohstoffe
Ähnliches klappt natürlich auch mit nachwachsenden Rohstoffen, die vor allem seit der Jahrtausendwende wieder stärker in den Blick gerückt sind. Einige der Verfahren sind aber viel älter, Viskose gibt es zum Beispiel bereits seit dem Ende des 19. Jahrhunderts. Dabei handelt es sich um Zellulose aus Holz, Bambus, Baumwolle und anderen Pflanzenmaterialien, die zunächst chemisch gelöst und anschließend durch Düsen gepresst mit Hilfe von Schwefelsäure wieder zu Viskose, Viskoseseide, Zellwolle, Rayon oder Kunstseide versponnen werden.
Aus diesen Fasern lassen sich nicht nur Textilien, sondern auch Hygieneprodukte wie der stark saugfähige Kern von Tampons herstellen. Drückt man die Viskoselösung nicht durch Düsen, sondern durch einen engen Spalt, entsteht eine Folie, die in der ersten Hälfte des 20. Jahrhunderts als Zellophan zum Verpacken von Lebensmitteln verwendet wurde. Mit relativ einfachen chemischen Reaktionen kann die Viskose in andere Werkstoffe umgewandelt werden. Hängt man zum Beispiel Nitratgruppen an, entsteht zunächst Zellulosenitrat, das mit Kampfer zu Zelluloid weiterverarbeitet werden kann. Mit organischen Säuren wie Essigsäure oder Propionsäure kann die Zellulose zu einer ganzen Reihe weiterer Kunststoffe verestert werden.
Eine weitere Möglichkeit bedient sich einer Art Vorratskammer, die Bakterien in schlechten Zeiten anlegen. Fehlen diesen Mikroorganismen wichtige Substanzen wie Stickstoff, Phosphor oder Sauerstoff, verknüpfen sie zum Beispiel Zucker zu langen Ketten eines Biopolyesters wie Polyhydroxy-Buttersäure, -Butyrat oder -Valerat. Diese Polyhydroxy-Fettsäuren oder nach dem Englischen PHA sind nicht nur wichtige Energiespeicher, sondern auch Kunststoffe, die von Bakterien synthetisiert werden und daher ein »Bio« vor ihrem Namen tragen dürfen. Daraus werden sowohl Folien zum Verpacken von Lebensmitteln als auch Fäden hergestellt, mit denen Ärzte zum Beispiel Operationswunden vernähen. Weil diese PHA-Fäden nach einiger Zeit vom Gewebe abgebaut werden, entfällt das Ziehen der Fäden.
Mikroorganismen produzieren Polymilchsäure
Mit der Polymilchsäure (PLA für das englische Poly-Lactid-Acid) ist ein weiterer, von Mikroorganismen produzierter Biopolyester zum Marktführer bei den Biokunststoffen aufgestiegen. Nach FNR-Zahlen gab es 2016 weltweit Kapazitäten für die Produktion von 2,05 Millionen Tonnen solcher Biokunststoffe, davon stellte PLA 10,3 Prozent. Ausgangsprodukt ist Stärke aus Weizen, Mais und anderen Pflanzen oder aus Zuckerrohr und Zuckerrüben gewonnener Zucker. Beide Substanzen werden von Bakterien zu Milchsäure fermentiert. Diese wird anschließend zu PLA polymerisiert.
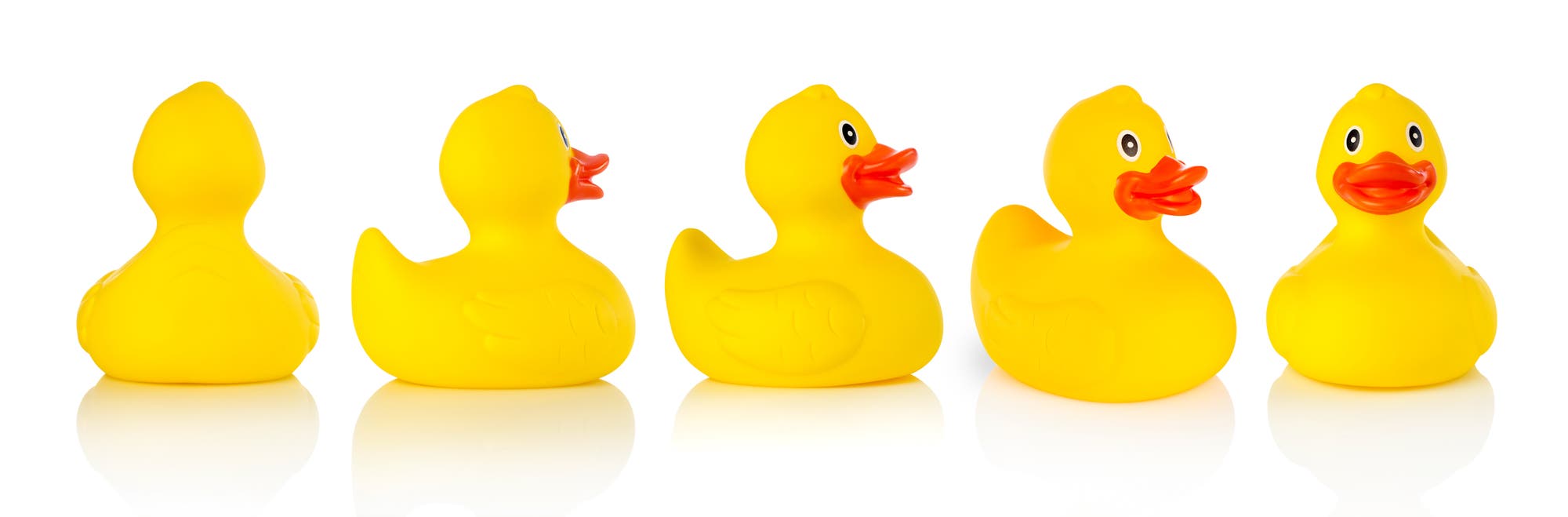
Je nach Beimischen verschiedener Additive oder anderer Kunststoffe ist dieses Polymer für eine ganze Reihe von Anwendungen tauglich: Mulchfolien für die Landwirtschaft, die sich nach dem Unterpflügen im Boden zersetzen, Obst- und Gemüseschälchen für den Lebensmittelhandel sowie Jogurtbecher, aber auch langlebige Produkte wie Handyschalen oder Schreibtischutensilien werden heute aus PLA angeboten.
Einer der großen Vorteile: Folien aus diesem Biokunststoff lassen Wasserdampf gut durch, PLA eignet sich daher sehr gut zum »atmenden« Verpacken von Lebensmitteln, Getränkeflaschen lassen sich aus diesem Material dagegen nur schwer herstellen.
Bio-PET mit Fruchtzucker und Stärke
Viele Erfrischungsgetränke werden daher wie bereits seit den 1970er Jahren immer noch in Flaschen aus dem Kunststoff Polyethylenterephthalat (PET) verkauft. PET wird normalerweise aus Ethylenglykol und Terephthalsäure hergestellt, die beide aus Erdöl gewonnen werden. Während Ethylenglykol zum Beispiel auch aus der Melasse von Zuckerrohr und damit nachhaltig zur Verfügung steht, gab es für die zweite Komponente bis vor Kurzem keine gute Bioalternative.
Das hat sich geändert, seit Ulf Prüße und seine Kollegen vom Thünen-Institut für Agrartechnologie in Braunschweig mit Hilfe eines neuen Extraktionsmittels die wichtige Basischemikalie 5-Hydroxymethylfurfural (HMF) preiswert aus Kohlehydraten wie dem Fruchtzucker Fruktose herstellen können, der aus Stärke gewonnen werden kann.
Aus HMF lassen sich die Bausteine einfach synthetisieren, aus denen die bisher meist aus Erdöl hergestellten Polyamid-, Polyester- und Polyurethan-Kunststoffe polymerisiert werden. Eine einfache Oxidation macht aus HMF die 2,5-Furandicarbonsäure (FDCA). Diese Substanz kann mit Ethylenglykol zum Polyethylenfuranoat (PEF) polymerisiert werden, dessen Eigenschaften sich mit PET messen können, von dem jedes Jahr mehr als 50 Millionen Tonnen produziert werden. Allerdings funktioniert die HMF-Synthese bisher nur im Labor, technische Pilotanlagen und damit der erste Schritt zu einer Vermarktung fehlen noch.
Linoleum erlebt ein Comeback
Das sieht bei Alkydharzen, häufig Bestandteil von Lacken, bereits anders aus. Hergestellt werden diese Substanzen aus mehrwertigen Alkoholen wie Glyzerin und Dicarbonsäuren wie der Bernsteinsäure, die häufig aus Erdöl gewonnen werden. Beide Stoffklassen können aber auch aus Pflanzenmaterialien produziert werden, entsprechende Lacke stehen daher bereits als Bioprodukte in den Verkaufsregalen. Mischt man Lein- und andere Pflanzenöle mit vernetzenden Substanzen, erhält man farblose und schnell trocknende Anstriche, die zum Beispiel für Druckfarben verwendet werden.
Ähnlich wird auch der Bodenbelag Linoleum aus Leinöl, Naturharzen, Kork- und Holzmehl sowie Jutegewebe als Trägerschicht und einigen weiteren Zusätzen für Farbe und andere Eigenschaften hergestellt. Und das bereits seit 1860. Zwar ließen Kunststoffe wie PVC ab den 1960er Jahren den Linoleummarkt praktisch zusammenbrechen. Seit den 1980er Jahren erlebt dieser Bodenbelag mit wachsendem Umweltbewusstsein seine Renaissance und wird wieder häufiger verlegt.
Genau wie für Alkydharze werden Dicarbonsäuren auch zur Herstellung von Polyamiden wie den althergebrachten Kunstfasern Nylon und Perlon verwendet. In diesem Bereich können daher nachwachsende Rohstoffe wie die Sebacinsäure aus Rizinusöl eingesetzt werden. Ähnliches gilt für Polyurethane, die als zentrale Komponente Polyalkohole besitzen, die aus Rizinus-, aber auch aus Raps-, Soja- oder Sonnenblumenöl gewonnen werden können. Aus diesen Kunststoffen entstehen zum Beispiel Schaumstoffe, aus denen Autositze und andere Produkte geformt werden können. Polyurethane sind aber auch wichtige technische Klebstoffe, die im Holz- und Automobilbau häufig eingesetzt werden. In einem von der FNR betreuten Projekt haben verschiedene Industrieunternehmen bis Ende 2018 gezeigt, dass als Grundstoffe auch heimische nachwachsende Rohstoffe wie Stärke, Saccharose und Rizinusöl dienen können.
Windeln aus Getreide
Ein wichtiger Pfeiler der Kunststoffwelt aus Erdölprodukten sind Polyacrylate, die in verschiedenen Formen eingesetzt werden, um zum Beispiel Plexiglas herzustellen. Forscher der Universität Duisburg-Essen können den Grundstoff für dieses Acrylglas inzwischen mit Hilfe eines Enzyms aus Zucker, Alkohol oder Fettsäuren herstellen, die allesamt aus Pflanzen gewonnen werden. Ein weiteres Verfahren zur Produktion von Acrylsäure aus Milchsäure, die von Bakterien aus Zucker oder Stärke synthetisiert wurde, haben Forscher der Universität Erlangen-Nürnberg entwickelt.
Aus den so gewonnenen Acrylaten entstehen Polyacrylate, von denen bisher weltweit rund fünf Millionen Tonnen jährlich aus Erdöl produziert und zu Lacken und Klebstoffen weiterverarbeitet werden. Da Polyacrylate Flüssigkeiten sehr gut aufsaugen, werden sie zum Beispiel für Hygieneprodukte wie Windeln und Damenbinden verwendet. Als Industriepartner beteiligte sich daher auch Procter & Gamble an diesem Projekt.
Der einfachste Kunststoff ist Polyethylen, von dem weltweit jedes Jahr rund 80 Millionen Tonnen hergestellt werden. Gewonnen wird der Grundstoff Ethylen dieses häufigsten Kunststoffes bisher aus Erdöl. Allerdings kann diese Chemikalie auch aus Bioethanol produziert werden. Brasilien hatte daher einen triftigen Grund, eine Produktionsanlage zu bauen, die aus Zuckerrohr erst Bioethanol und anschließend bis zu 200 000 Tonnen Ethylen im Jahr herstellen kann. Dieses Bioethylen kann auch für die Produktion von nachhaltigerem PVC verwendet werden. Obendrein eignet sich Bioethanol aus Zuckerrohr und anderen Pflanzen zur Produktion von Polypropylen und damit von einem sehr wichtigen Kunststoff, von dem bisher im Jahr 44 Millionen Tonnen aus Erdöl produziert werden.
Pommes frites und Biokunststoffe
Noch besser wäre es natürlich, solche Biokunststoffe nicht aus eigens dafür angebauten Nutzpflanzen wie Zuckerrohr oder Zuckerrüben, sondern aus Abfällen herzustellen, die bei der Produktion von Nahrungsmitteln anfallen. Eine Pilotanlage in den Niederlanden verwendet zum Beispiel das Abwasser, das beim Schneiden von Kartoffeln für Pommes frites anfällt, um aus der darin enthaltenen Stärke Kunststoffe herzustellen.
Biokunststoffe scheinen also auf dem Vormarsch zu sein. Trotzdem erreichen sie bei einer jährlichen Weltproduktion von rund 330 Millionen Tonnen Kunststoffen derzeit allenfalls einen Anteil von kümmerlichen zwei Prozent. Die FNR rechnet dagegen damit, dass nach heutigem Stand der Technik insgesamt 90 Prozent aller Kunststoffe nachhaltig hergestellt werden können. Da nachhaltige Produkte bei Herstellern und Verbrauchern gleichermaßen beliebt scheinen, muss es einen handfesten Grund für die bisher allenfalls magere Biokunststoffbilanz geben.
Dieser Grund sind die Kosten: Aus Erdöl produzierte Kunststoffe gibt es schließlich bereits seit Jahrzehnten, die Produktionstechniken sind ausgereift, und sie werden in riesigen Mengen hergestellt. Die Entwicklungskosten sind also längst abgezahlt, die Massenproduktion gepaart mit einer optimierten Technik garantiert niedrige Preise. Bei vielen Biokunststoffen dagegen greifen diese Vorteile nicht. Sie können sich daher nur durchsetzen, wenn sie handfeste Vorteile bieten. Das könnte zum Beispiel eine atmungsaktive Biofolie sein, in der Lebensmittel besser halten.
Wichtig sind auch die Wünsche der Verbraucher, von denen viele auf Nachhaltigkeit Wert legen. Der Hersteller Coca-Cola hat darauf bereits reagiert und möchte bis zum Jahr 2020 seine Getränke-PET-Flaschen auf Basis pflanzlicher Rohstoffe herstellen. Allein auf diesem Weg aber dürften Massenkunststoffe den Weg zur Nachhaltigkeit kaum schaffen. Gefragt ist daher die öffentliche Hand: Behörden, Universitäten, Schulen oder auch die Deutsche Bahn könnten zum Beispiel gezielt Produkte auf Biobasis von der Handyschale bis zur Kaffeemaschine anschaffen.
Mehr als zwei Drittel der Rohstoffe importiert
Viel günstiger sieht die Marktsituation für Produkte auf Biobasis übrigens aus, wenn man den Blick von den Kunststoffen auf die gesamte Palette der chemischen Industrie von Schmierstoffen über Lacke und Druckfarben bis zu Reinigungsmitteln und Medikamenten erweitert. 2016 hat die chemische Industrie in Deutschland nach Angaben der FNR insgesamt 20,6 Millionen Tonnen organischer Rohstoffe eingesetzt. Davon waren mit 2,7 Millionen Tonnen immerhin rund 13 Prozent biobasiert, die restlichen 87 Prozent kamen aus Erdöl.
Den Löwenanteil bei diesen organischen Rohstoffen auf Biobasis stellten mit 43 Prozent Fette und Öle, dazu kamen 14 Prozent Chemiezellstoff, elf Prozent Stärke und mit insgesamt 156 000 Tonnen rund sechs Prozent Zucker sowie etliche weitere Rohstoffe. Damit sind diese Rohstoffe von Äckern und Wäldern längst den Kinderschuhen entwachsen und zu einer entscheidenden Stütze der chemischen Industrie geworden.
Allerdings kommt nur ein knappes Drittel von ihnen aus Deutschland, mehr als zwei Drittel werden importiert. Andererseits werden von den daraus hergestellten Produkten bei Weitem nicht alle in Deutschland verkauft, ein erheblicher Anteil geht in den Export. Die Frage nach der Verfügbarkeit stellt sich natürlich trotzdem. Beanspruchen die biobasierten Rohstoffe vielleicht einen zu großen Anteil der Agrar- und Forstflächen? Verdrängen sie eventuell den Anbau von Nahrungsmitteln? Gefährden Mais und Flachs etwa die Artenvielfalt?
Reichen die Äcker?
Ein Blick auf die Verwendung der fossilen Rohstoffe zeigt rasch, dass diese Fragen bei Energiepflanzen weit wichtiger als bei einer stofflichen Nutzung sind: Gerade einmal fünf Prozent von Kohle, Erdöl und Erdgas werden nach Angaben des Verbands der Chemischen Industrie stofflich verwertet, 16 Prozent werden zu Kraftstoffen verarbeitet, die restlichen 79 Prozent werden energetisch genutzt und liefern zum Beispiel Wärme und Elektrizität. Die FNR nennt ähnliche Zahlen für Erdöl, von dem drei bis vier Prozent zu Kunststoffen weiterverarbeitet werden, während der übergroße Rest in Motoren und Kraftwerken verfeuert wird.
Diese Zahlen spiegeln sich nach den Angabe des Statistischen Bundesamts schon heute auf deutschen Äckern und in den hiesigen Wäldern wider: Von insgesamt 35,7 Millionen Hektar Landesfläche entfallen 7,6 Millionen Hektar auf Siedlungen, Verkehrs- und Wasserflächen und das Umland dieser Gebiete, auf 11,4 Millionen Hektar wachsen Wälder, während Bauern die restlichen 16,7 Millionen Hektar bewirtschaften. Auf 60 Prozent dieser landwirtschaftlichen Nutzfläche wächst Viehfutter, auf 22 Prozent werden Nahrungsmittel für Menschen geerntet, während Energiepflanzen weitere 14 Prozent beanspruchen. Die restlichen vier Prozent Fläche teilen sich Brachen und Industriepflanzen zu gleichen Teilen.
Von den insgesamt 300 000 Hektar, auf denen 2017 in Deutschland Industriepflanzen wuchsen, lieferten 142 200 Hektar Pflanzenöle, 128 000 Hektar Stärke, 15 400 Hektar Zucker, 12 000 Hektar Arznei- und Farbstoffe und 1500 Hektar Pflanzenfasern.
Brot oder Biowindeln?
Wenn der Landwirt seine Felder bestellt, weiß er oft noch gar nicht, was aus seiner Ernte einmal wird. Schließlich beeinflussen Witterung und mögliche Wetterkapriolen zum Beispiel ein Getreidefeld erheblich. Gerade die Inhaltsstoffe von Weizenkörnern, die über die Qualität des Mehls entscheiden, können sich bei entsprechenden Bedingungen stark verändern. Da Bäcker verständlicherweise großen Wert auf eine möglichst gute Backeigenschaft legen, ist der Bauer nach der Ernte vielleicht ganz froh, wenn er für sein Getreide mit geringerer Backqualität noch einen akzeptablen Preis auf dem Markt für Industriestärke erzielen kann.
Vor einer ähnlichen Situation steht auch der Zuckerrübenbauer: »Zucker gibt es eigentlich reichlich«, berichtet der FNR-Experte Dietmar Peters. Da kann es den Bauern nur recht sein, wenn aus dem Zucker ihrer Rüben auch der saugfähige Polyacrylatkunststoff für Windeln oder Damenbinden produziert werden kann.
Wenn Sie inhaltliche Anmerkungen zu diesem Artikel haben, können Sie die Redaktion per E-Mail informieren. Wir lesen Ihre Zuschrift, bitten jedoch um Verständnis, dass wir nicht jede beantworten können.